
Совместное же производство с группой Sollers (читай Северсталь) было образовано в феврале 2011 года - Соллерс тогда отказался от проекта с Фиатом.
В начале июле на первом заводе "Форда" в России, расположенном во Всеволожске, официально начали производить обновлённую модель Фокуса. Благодаря этому событию удалось проникнуть на завод и ознакомиться с производством.
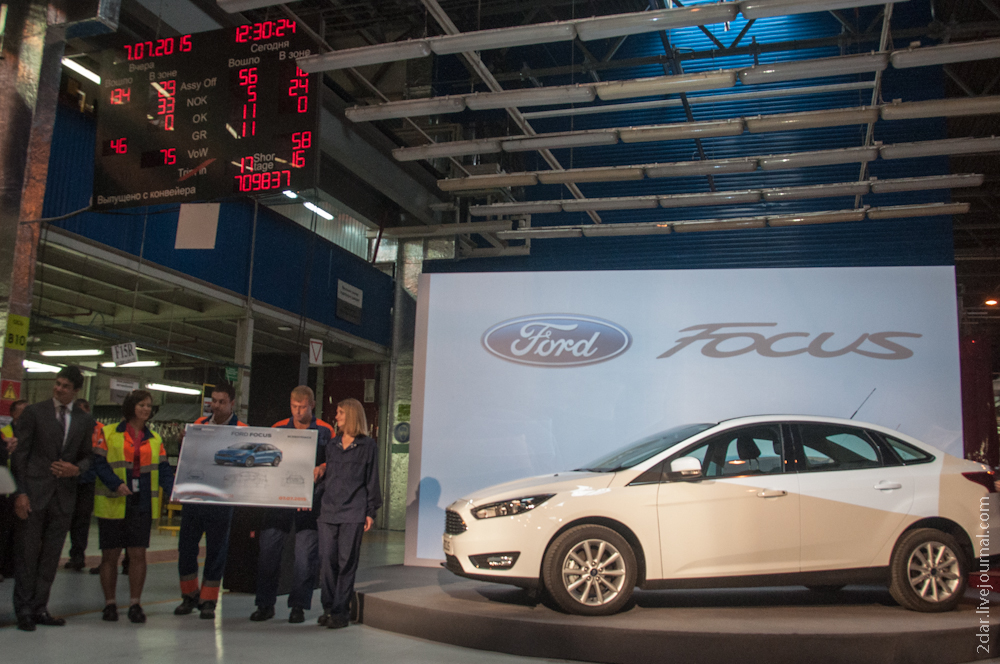
Как видно за 13 лет удалось собрать 709 837 автомобилей. Это Фокусы и Мондео в трёх типах кузовов: седан, хетч и универсалы. Сейчас уже освоено третье поколение некогда народных Фокусов. Официально открыть производство доверили наиболее успешным сотрудникам завода.
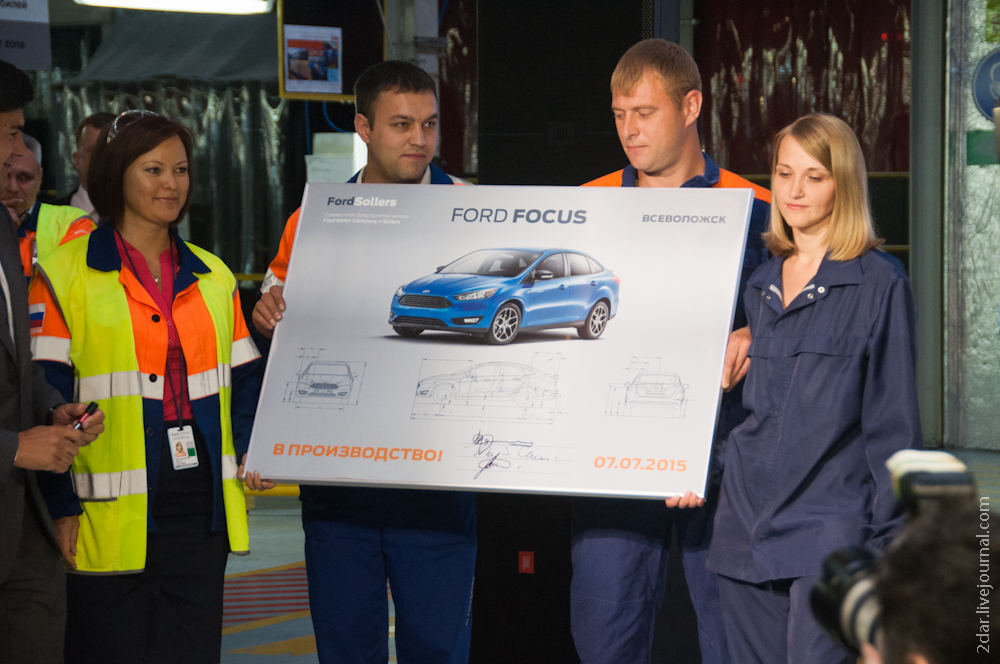
Хотя, конечно, без ВИПов не обошлось. Присутствовал президент CEO Ford Sollers Тед Канниссам, первый вице-президент Адиль Ширинов. Губернатор Ленобласти был так же, причём по его долгой речи не у одного меня создалось впечатление, что выступает не губернатор, а менеджер Форда или даже пиарщик автогиганта. Казалось бы, причём тут
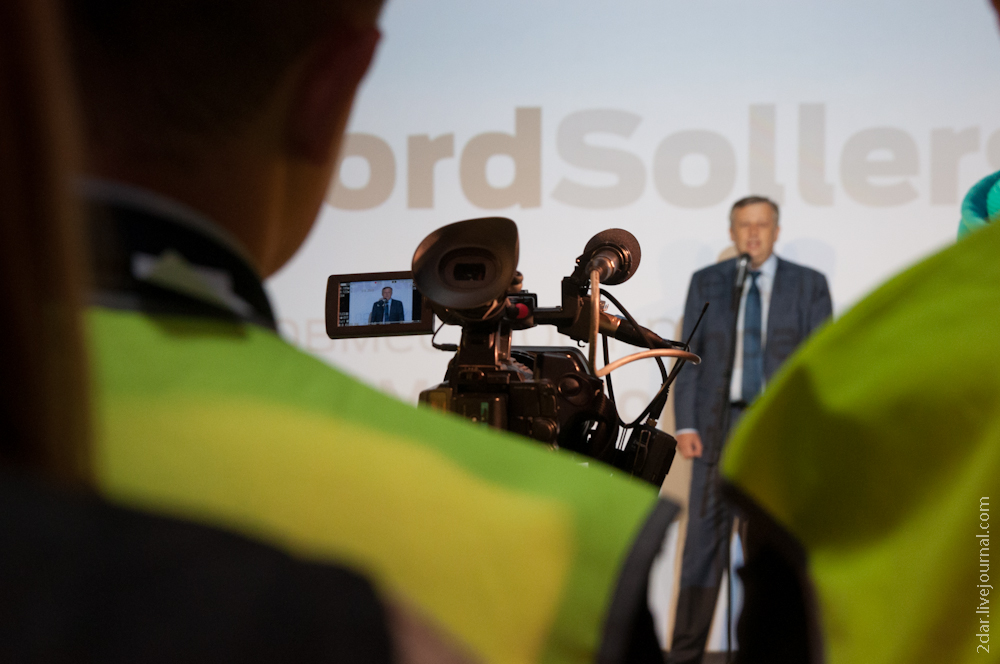
Александр Дрозденко покатался так же на Фокусе и несколько неуверенно припарковал его задним ходом: - "Испытывали новую систему активной помощи при парковки" - пояснил он. С этой системой - Active Parking Assist, а также многочисленными другими новшествами и плюшками новой модели можно ознакомиться на страничке: http://newfocus.ru/
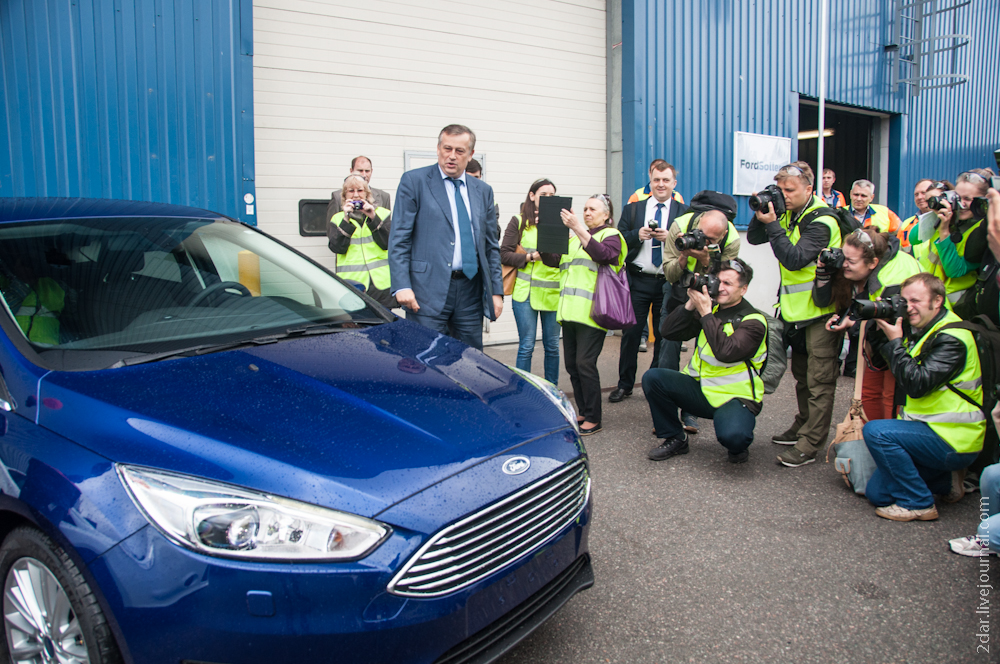
Однако вернёмся на завод и посмотрим на само производство. Наиболее целостную картину можно составить не двигаясь по цехам, а посмотрев на всё хозяйство сверху - вот например на Плане завода (картинка кликабельна - откроется с максимальным разрешением и можно будет прочитать легенду)
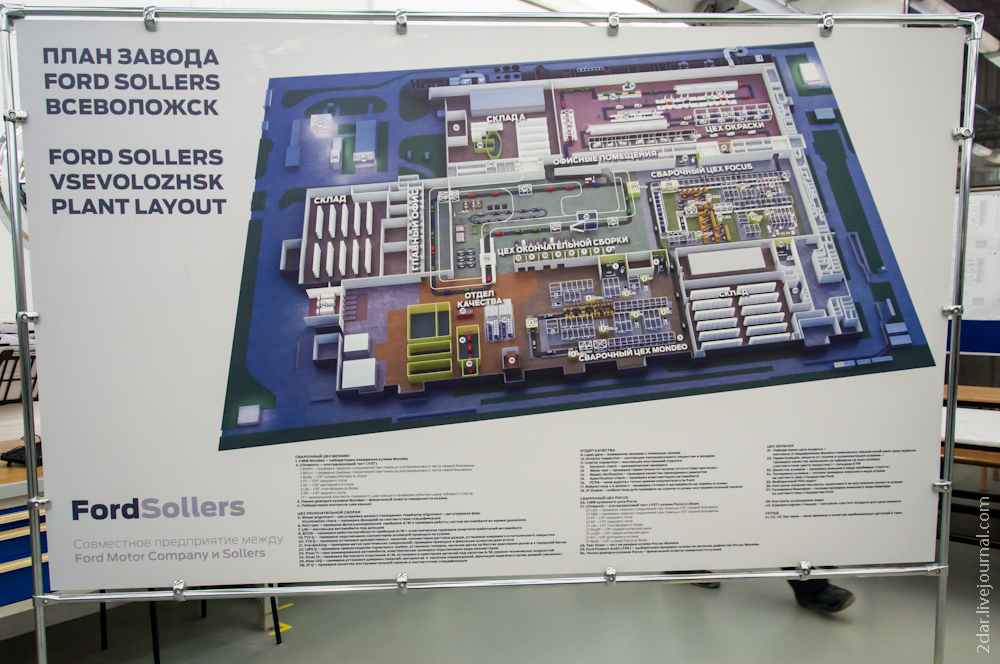
Итак, начинается всё со сварки. Кузовной цех это конвейер в 359 метров длинны на которую с тактом 165 секунд собирают кузов за 3 часа 10 минут. Собственно кузовных цеха два: для Фокуса и Мондео. Вначале сваривают отдельные детали в крупные узлы. На специальных станках снабжённых гидравлическими зажимами устанавливаются детали, которые вручную сваривают, например, в заднюю панель кузова.
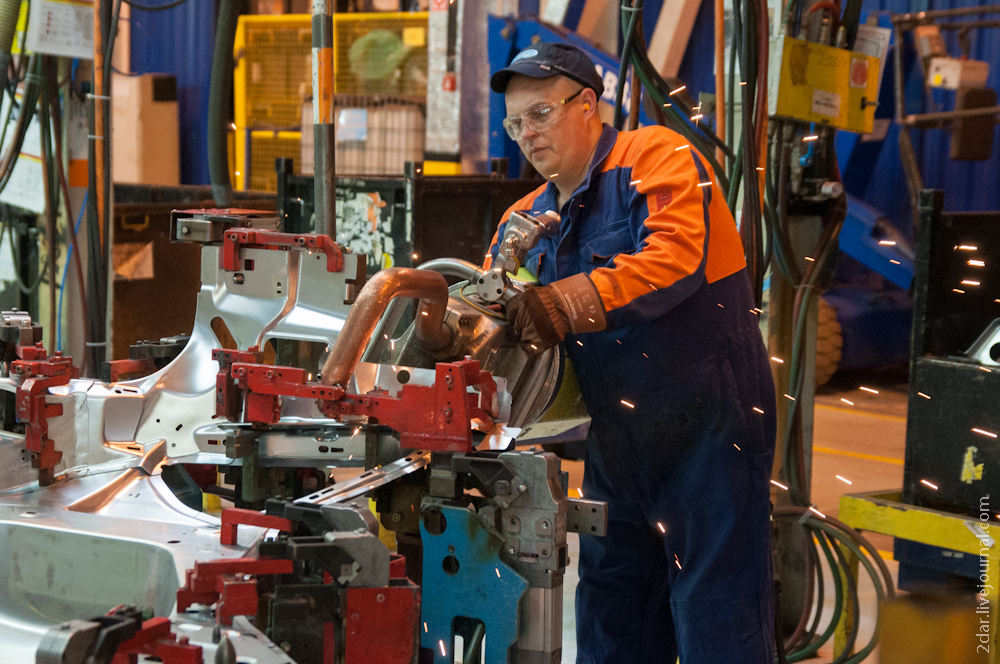
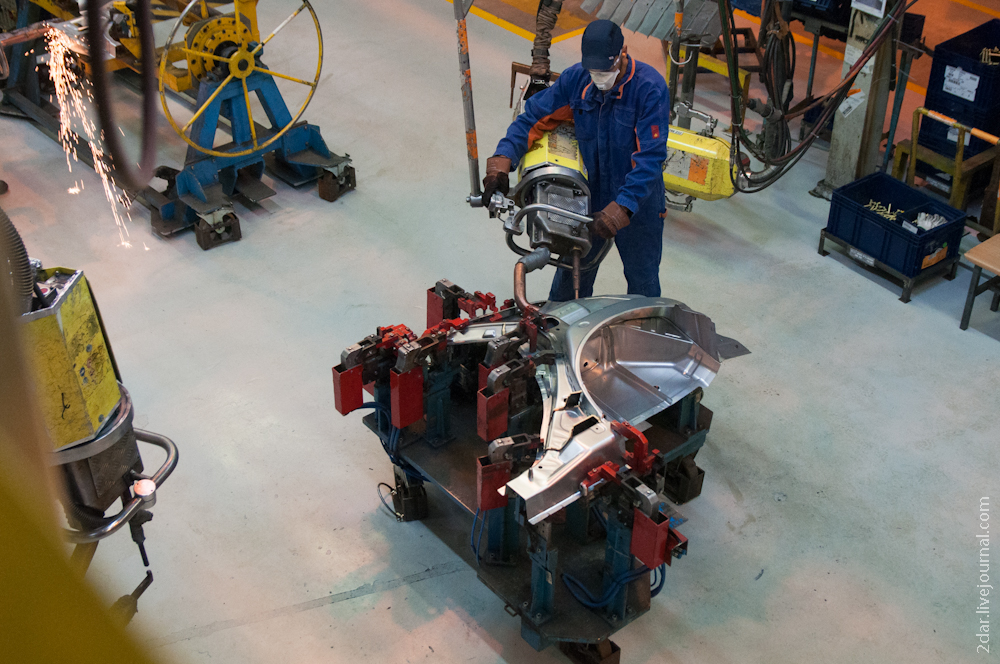
Далее участок роботизированной сварки - принцип тот же самый, только узлы крупнее. Роботы Kuka вертят и крутят боковины кузова будто они картонные.
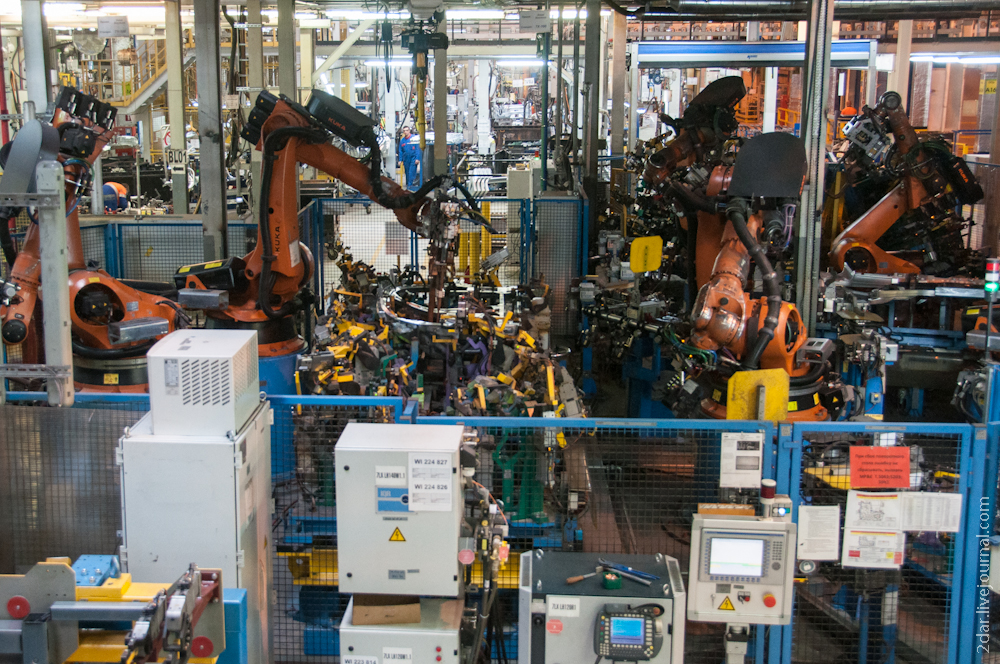
И третий этап окончательная проварка сварных швов...
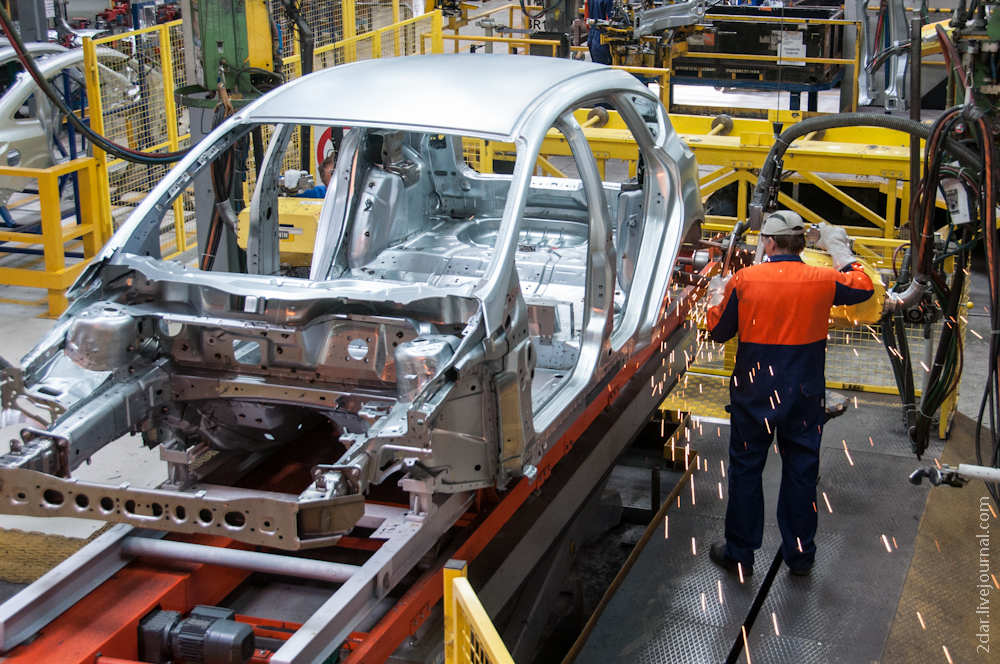
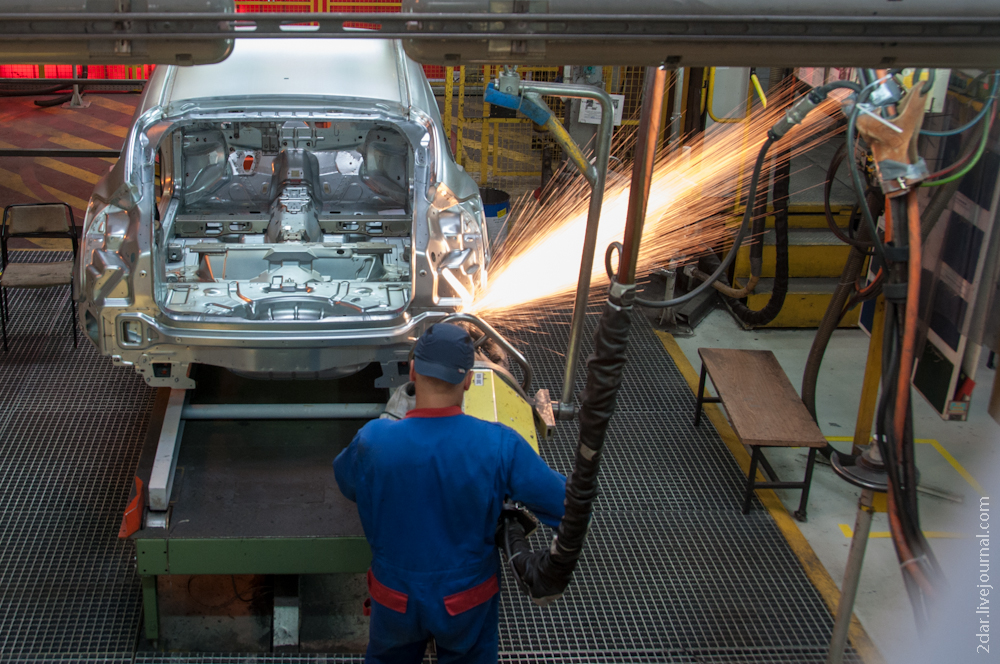
и «навеска» наружных деталей кузова.
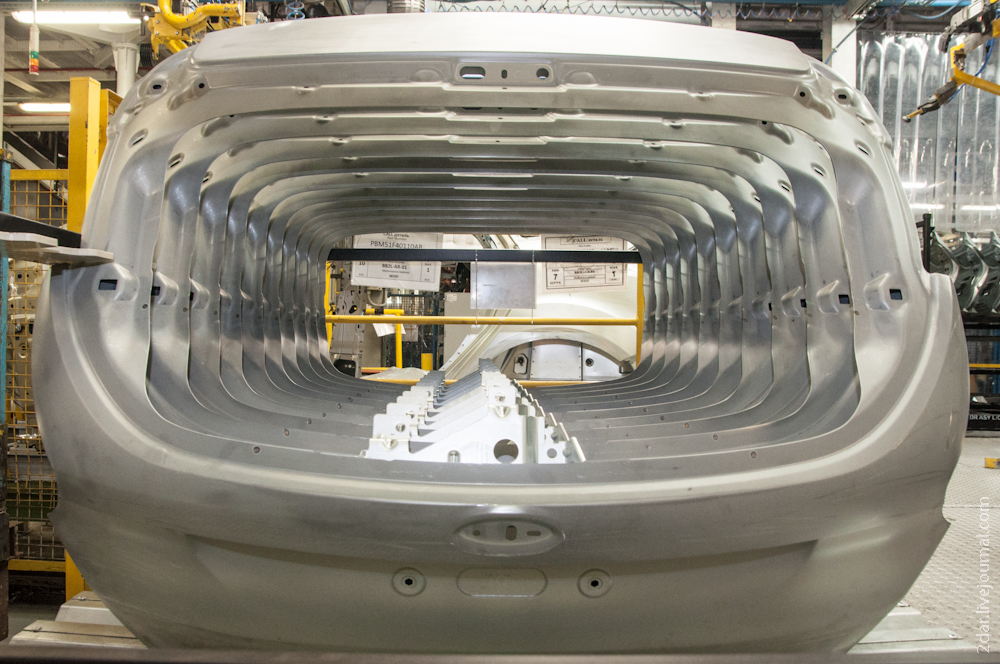

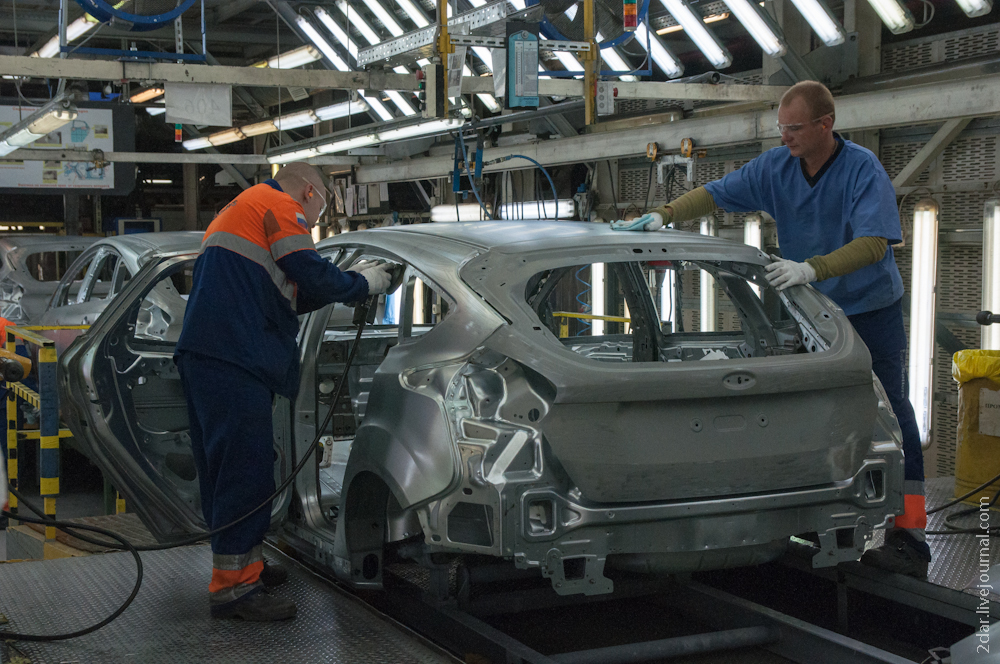
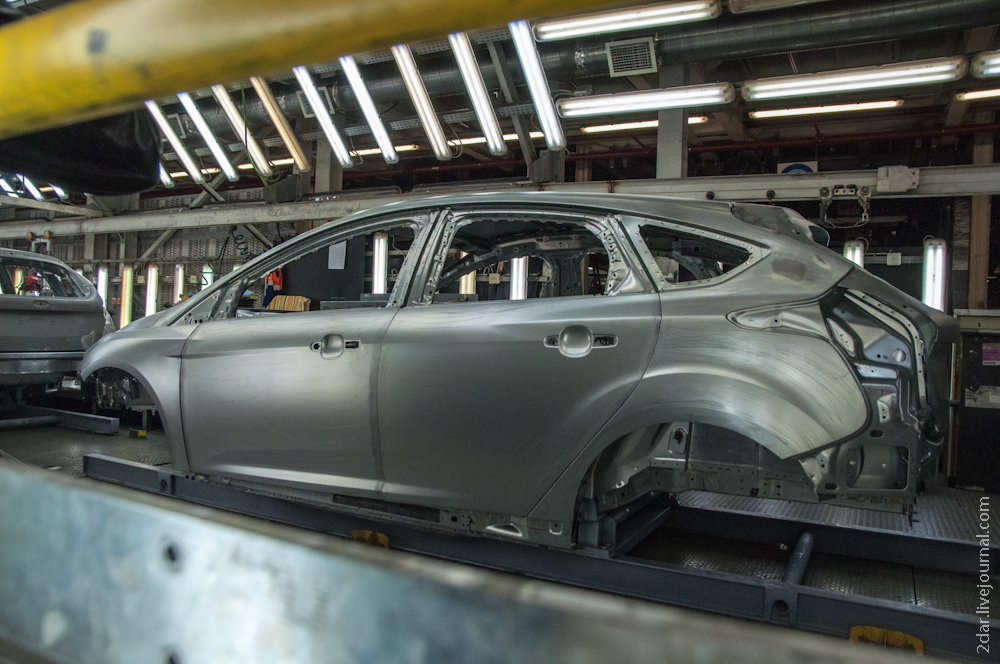
Полученные кузова тщательно контролируют несколько отделов. Здесь, например, проверяется тщательно геометрия кузова.
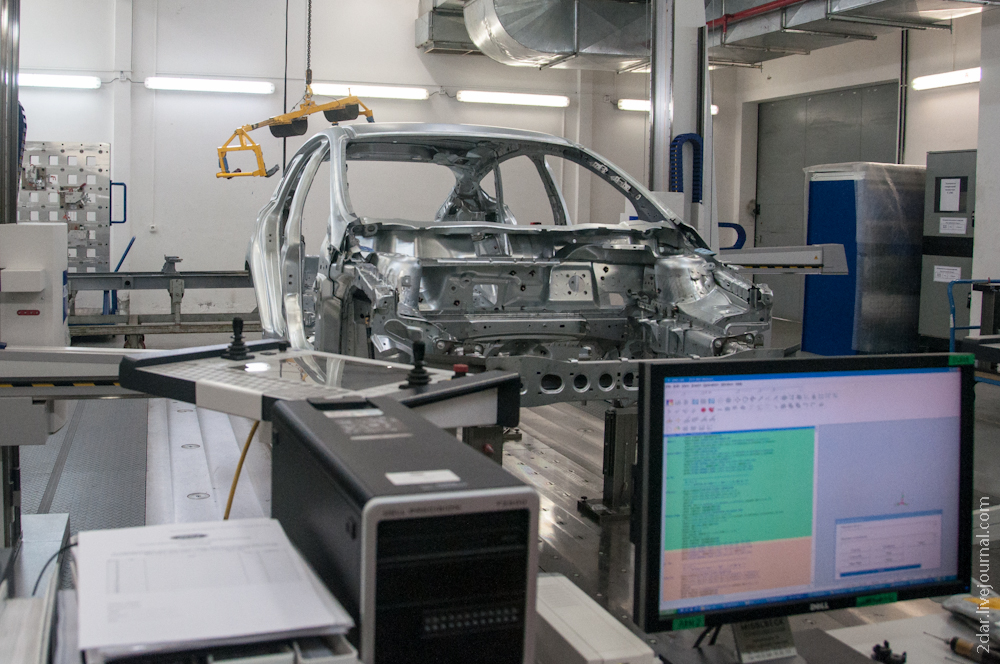
А здесь качество швов - механическим и ультразвуковым способами.
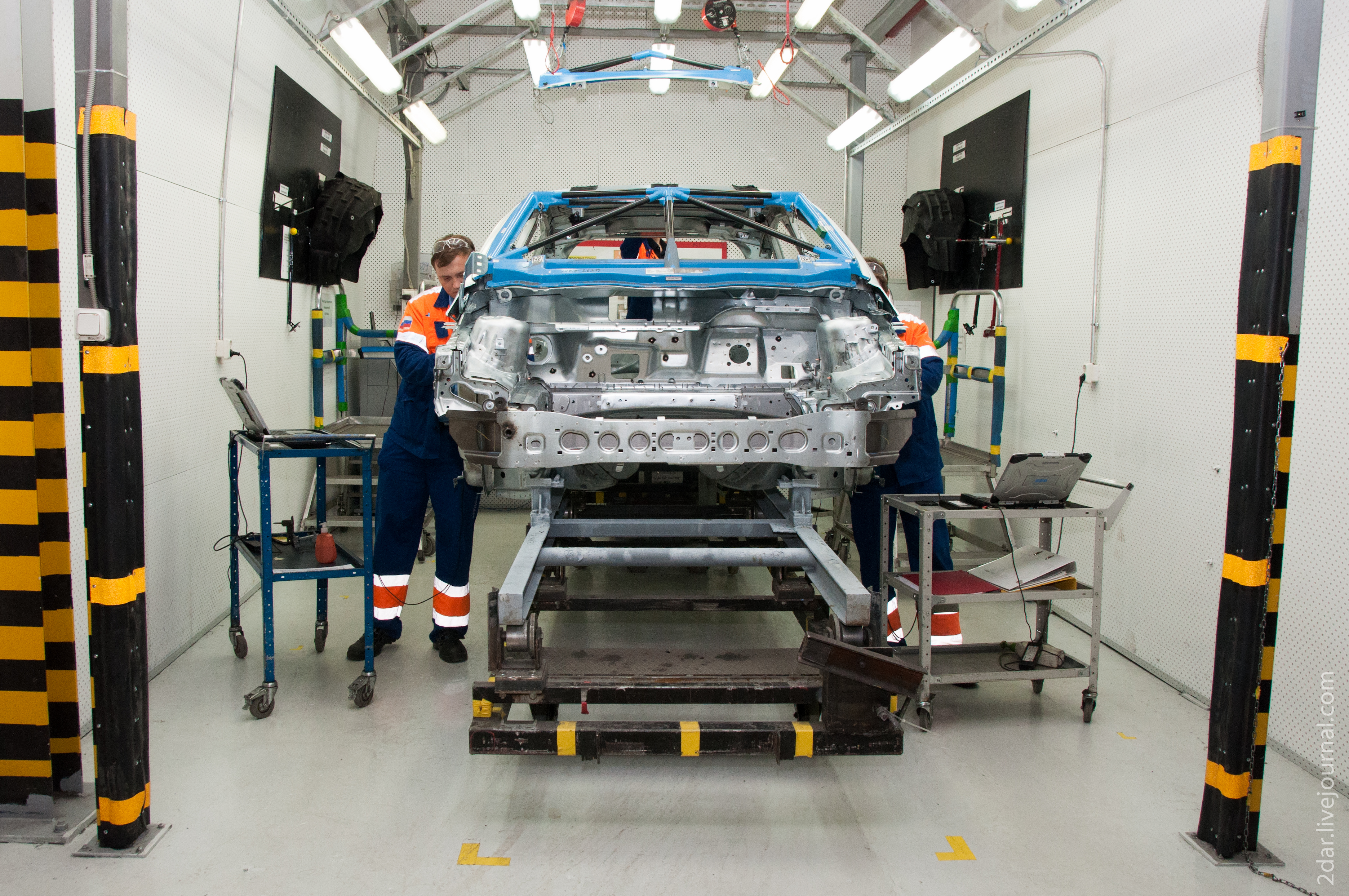
Далее цех окраски. К сожалению его не удалось осмотреть - там строгие нормы допуска. Но, на схеме хорошо видны основные этапы. Кузов окрашивается за 4 часа 33 минуты пойдя через 93 станции.
И собственно дальше непосредственная сборка - навешивание на голый кузов всей начинки и облицовки, начиная жгутами проводов и облицовкой пола.
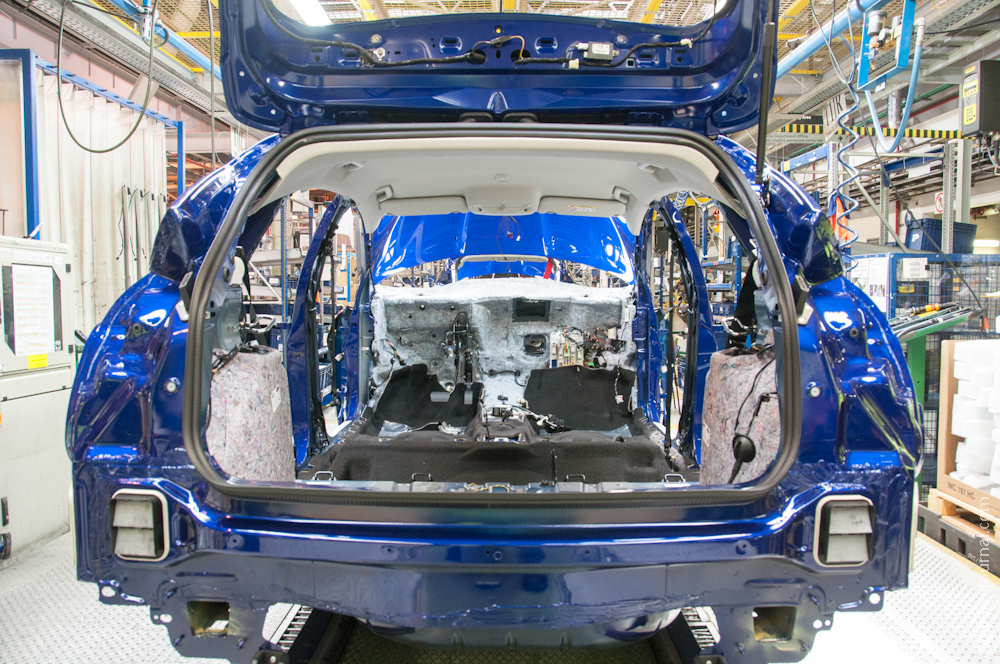
Естественно сейчас, в нашем потребительском настоящем, на конвейере почти нет одинаковой машины: разные комплектации, силовые установки, КПП предполагают множество вариаций. Сборщик получает информацию из штрихкодов которые сопровождают автомобиль
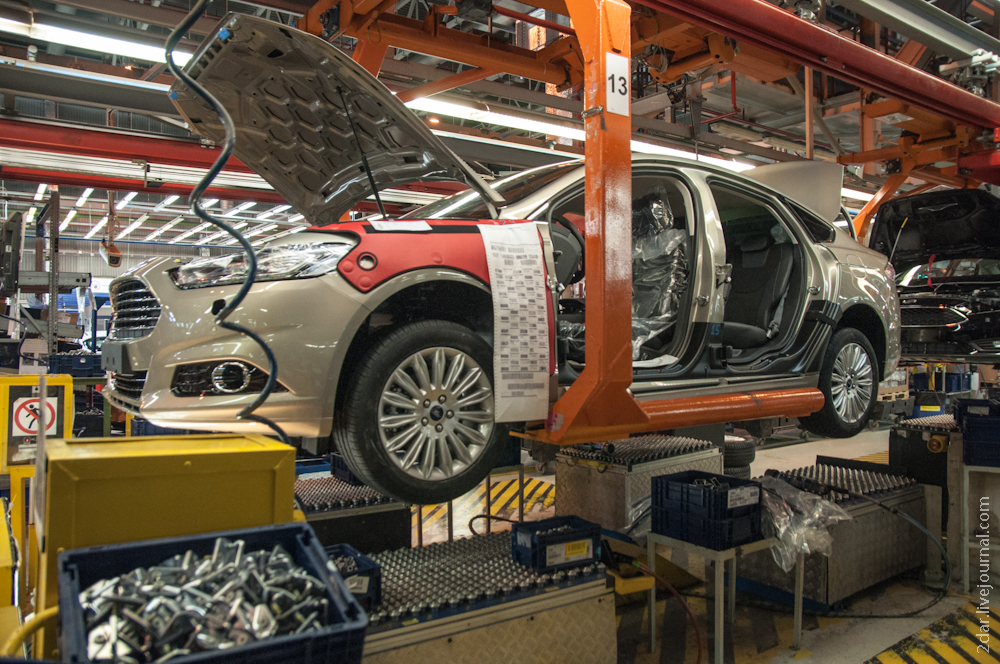
Увы, увидеть "свадьбу" - соединение двигателя с кузовом не удалось - слишком далеко на конвейере была расположена это операция. А на снимке станция установки колёс.
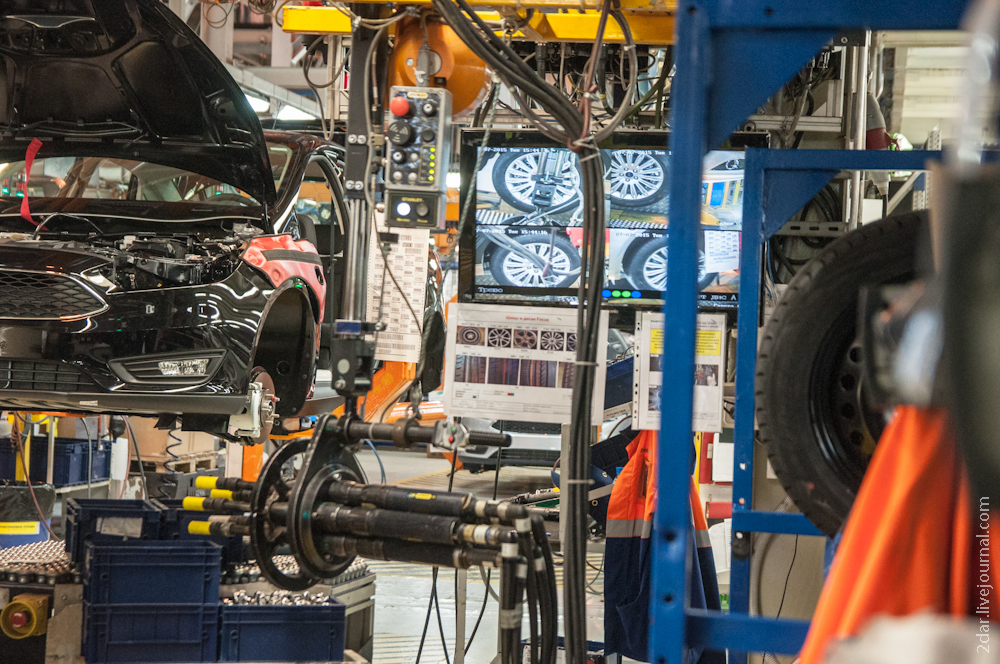
2 часа 42 минуты нужно чтобы превратить голый окрашенный кузов в готовый продукт. 226 станции на 432 метров - любители цифр - это строчка для вас.
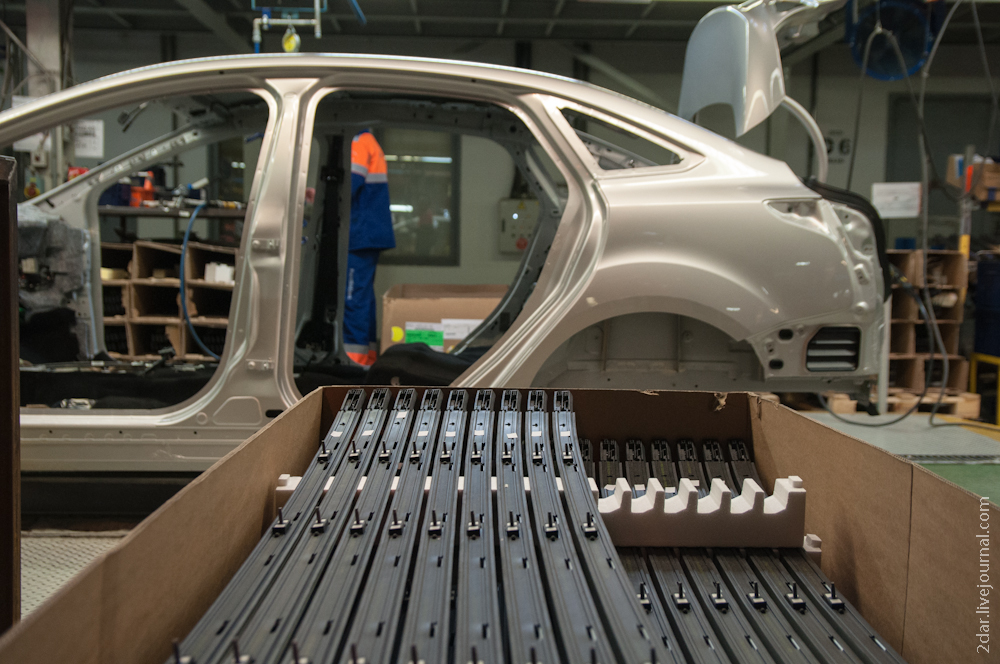
Системе качества на Форде уделяют большое внимание. Ещё бы - отзывные компании никому не нужны От потребителей поступает непрерывная обратная связь и некоторые предложения имеют шансы быть доведённой до внедрения. Аналогично и от сотрудников производства рацпредложения по повышению качества, безопасности и эффективности принимают во внимание.

впрочем для "наших людей" лучше доходит не зарубежный стиль инфографики, а наш шершавый язык плаката.
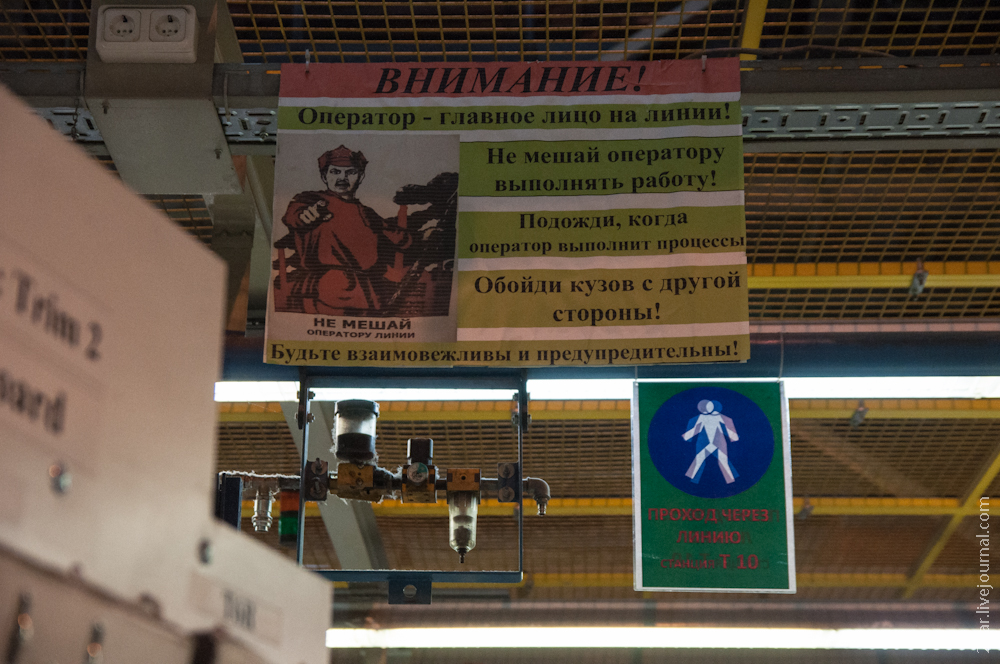
И, наконец, настало время многочисленных финальных проверок. Начинают с осмотра кузова.
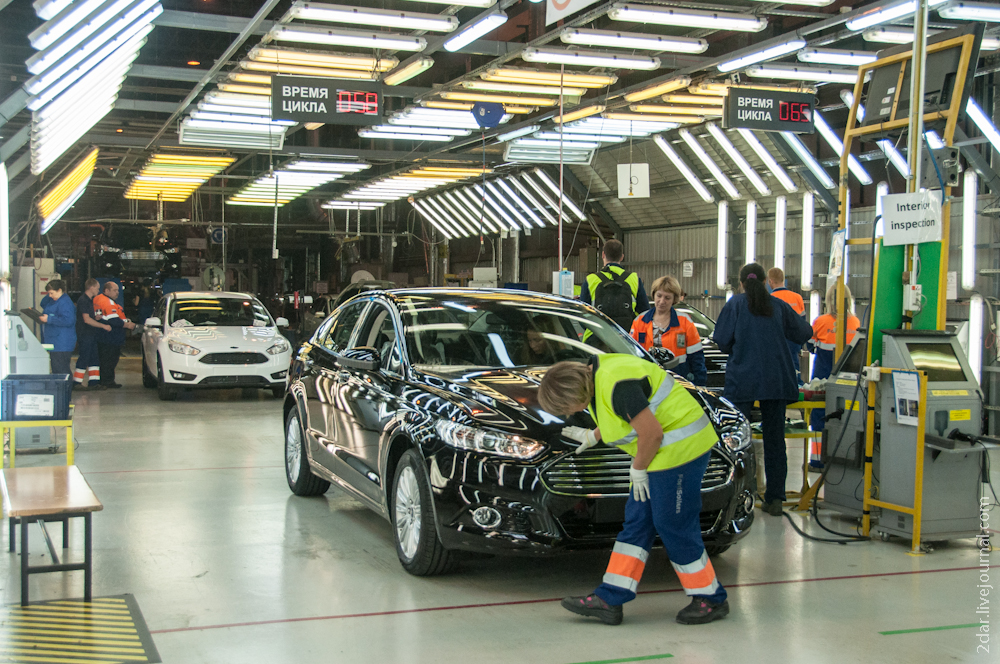
проверяют герметичность.
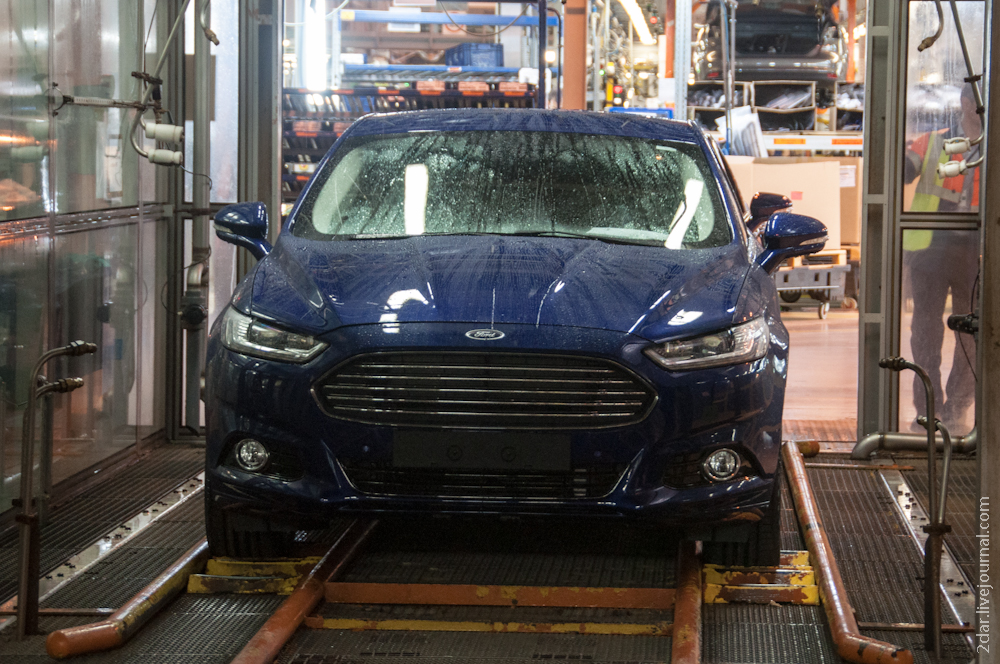
и много чего ещё. В том числе и прогоняют через такой вот миниполигон имитирующий разные виды дорожных покрытий. Всё - можно ехать на склад готовой продукции.
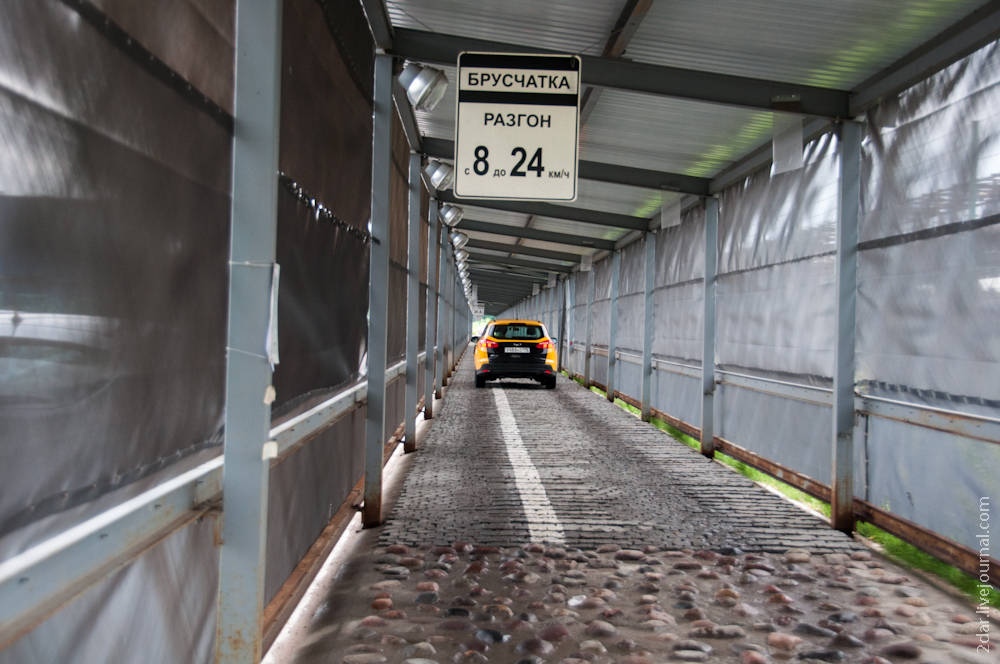