Действуй злее гранатой, автоматом, ножом и лопатой!
Свежеиспечённый классный специалист ВС РФ.

1.Взлёты тройками.
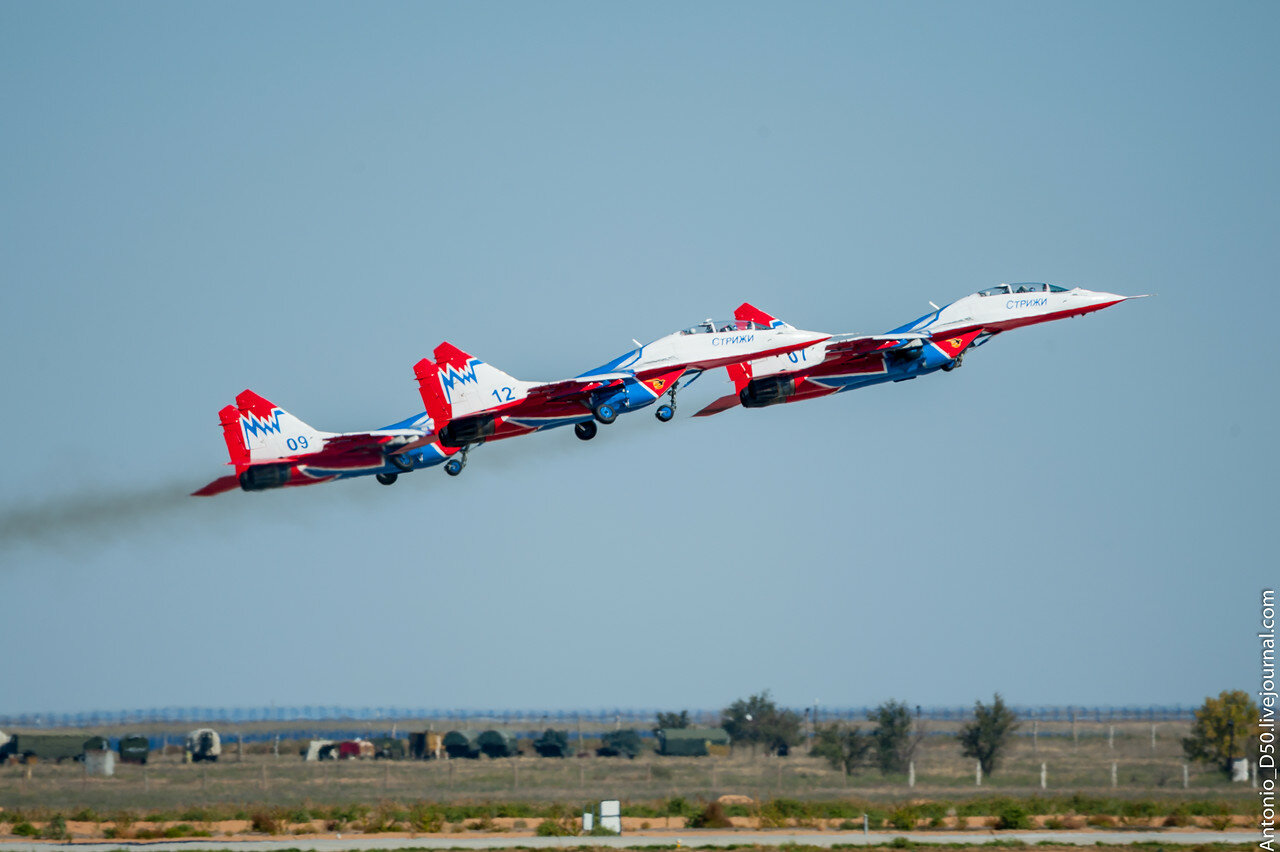
2.

3.

4.

5.Фирменные кренделя от МиГов.
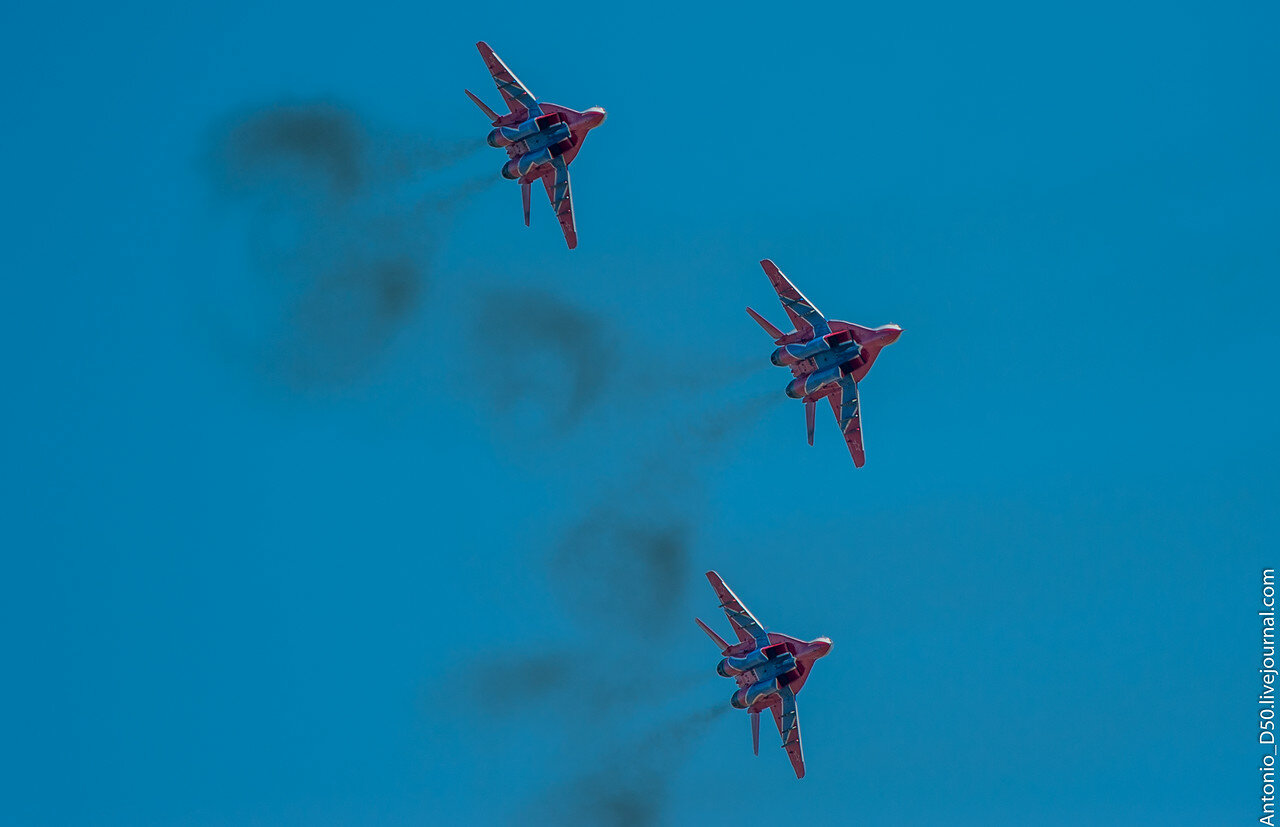
6.

7.Выстроились.
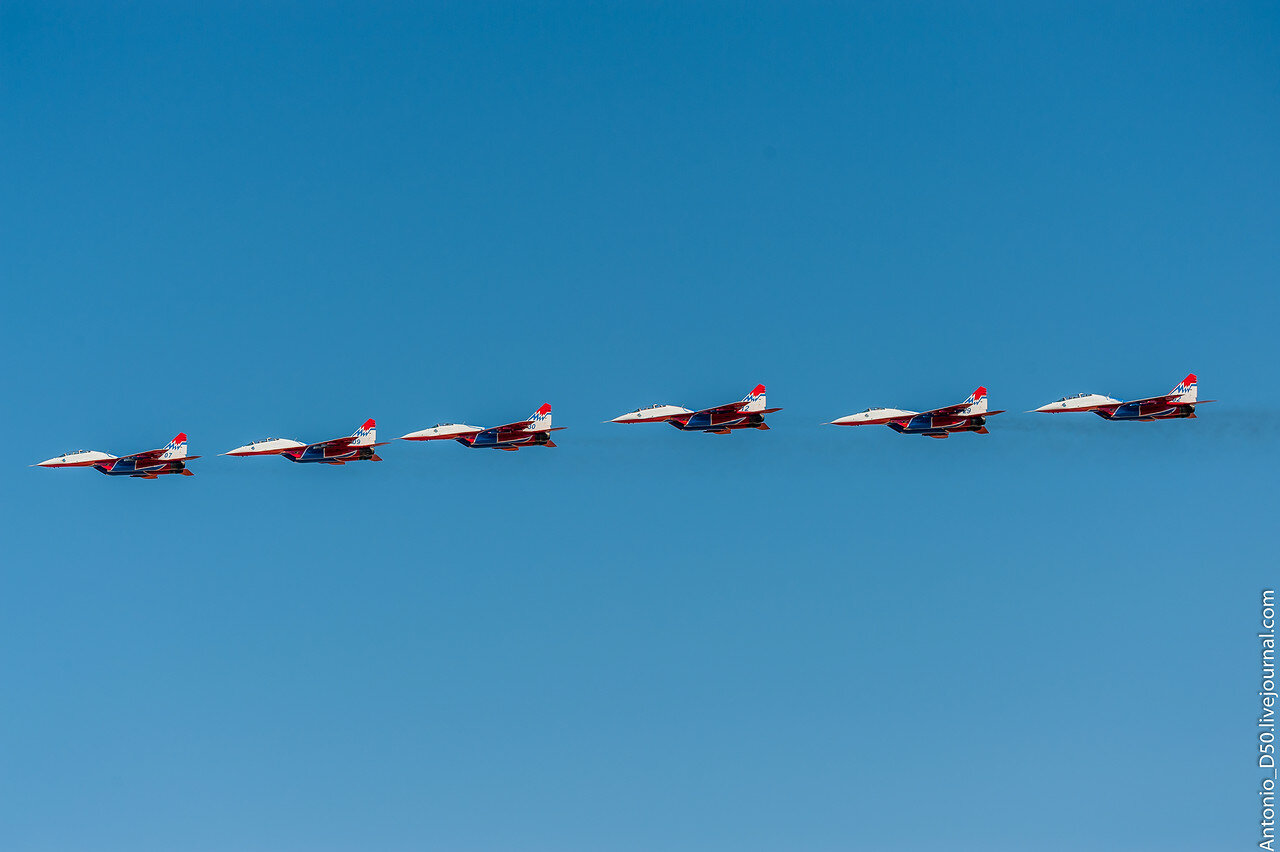
8.
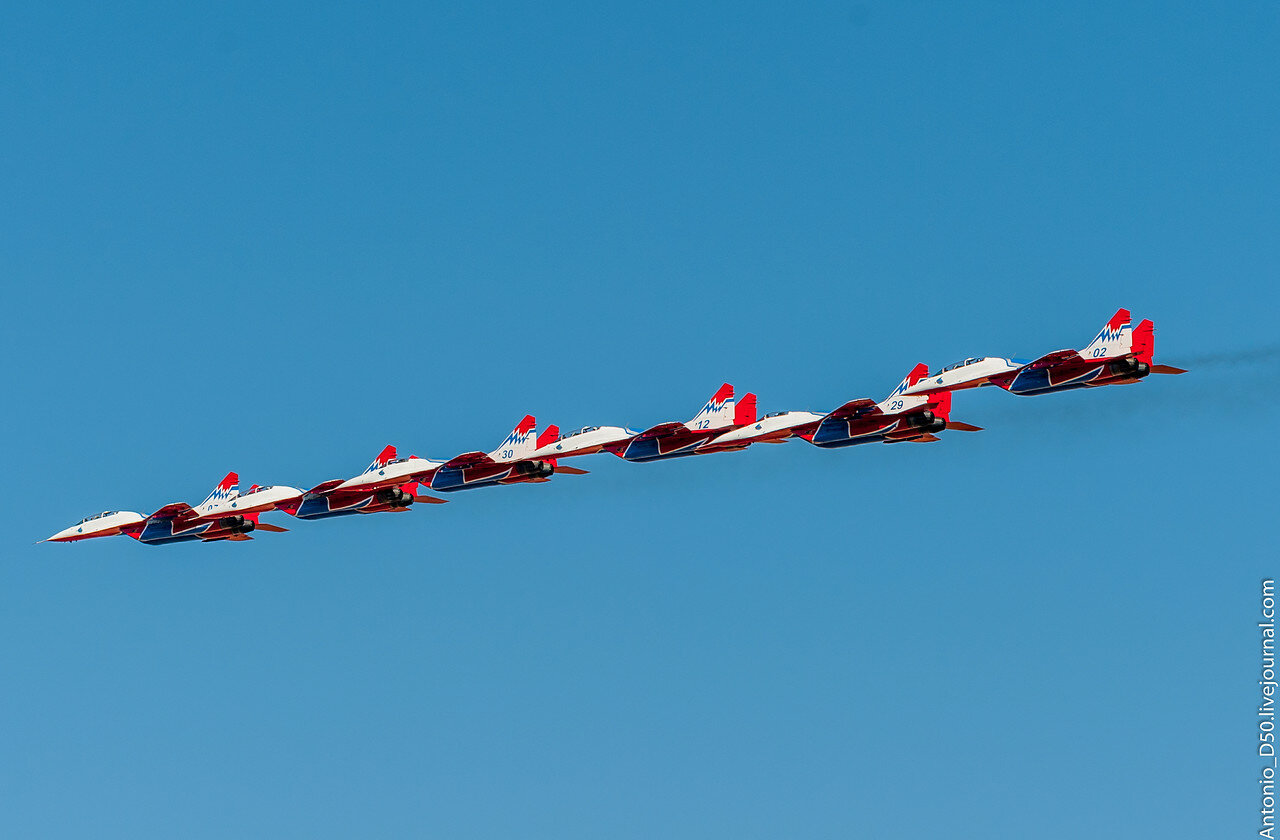
9.Пирамида.

10.

11.

12.
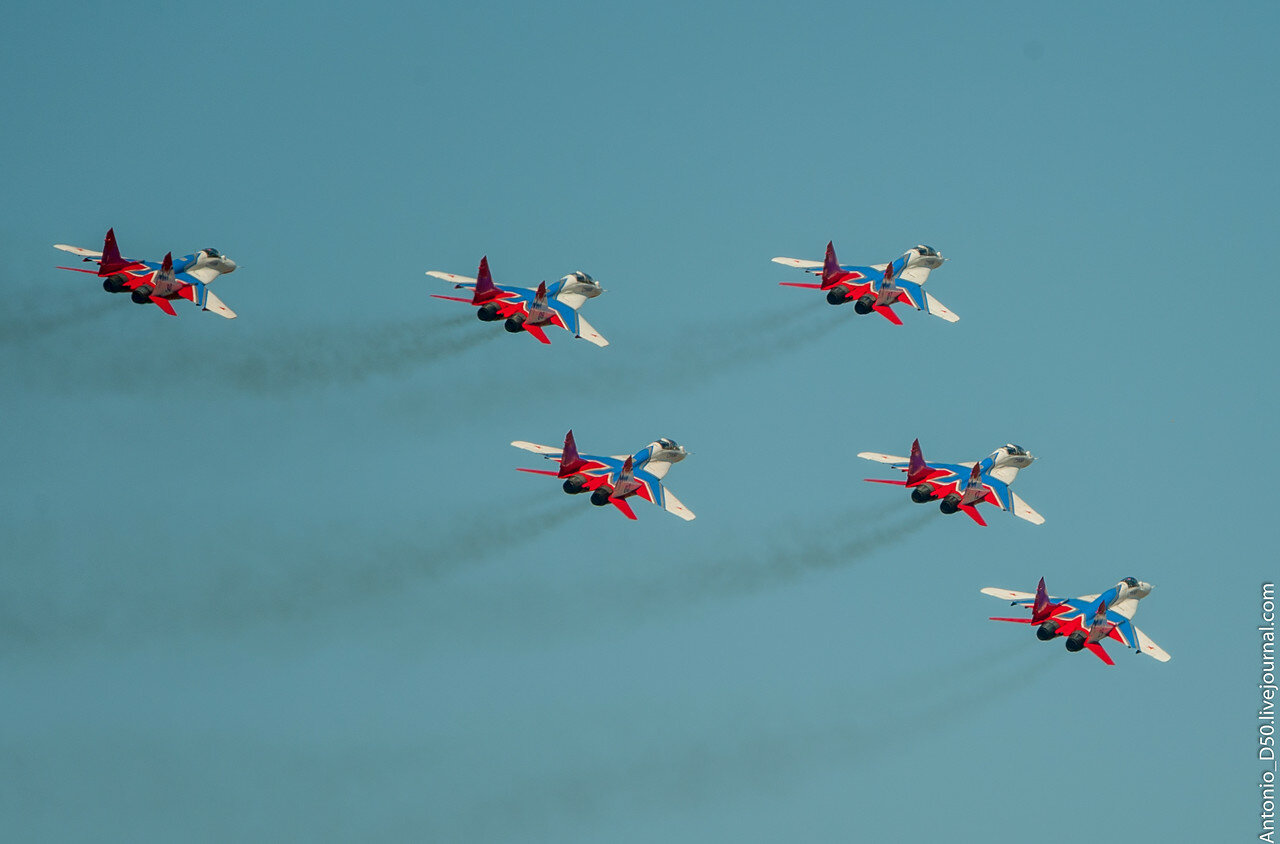
13.

14.

15.Роспуск номер один.

16.

17.

18.Стрела.
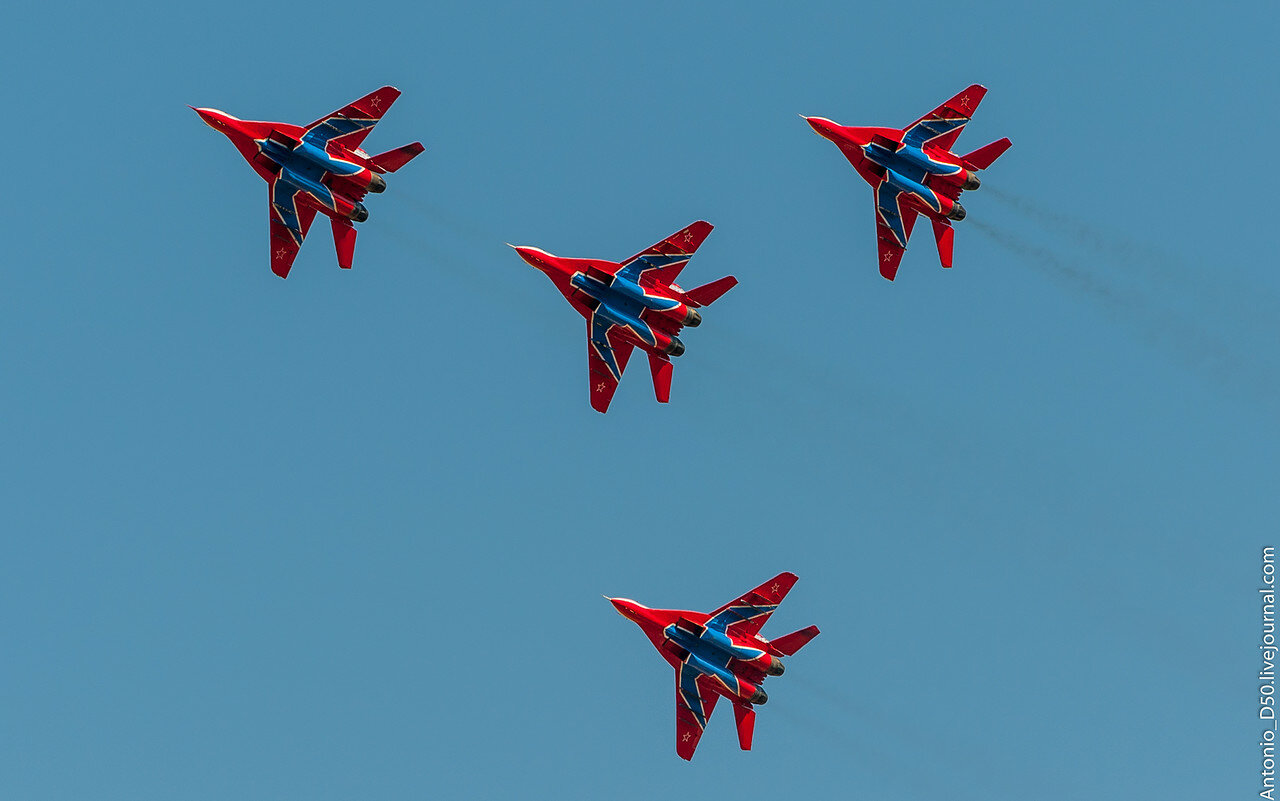
19.

20.

21.

22.Роспусе номер два.

23.

24.Ножницы.

25.

26.Зеркало.

27.Соло-пилотаж на форсажных режимах.

28.

29.

30.

31.

32.

33.

34.
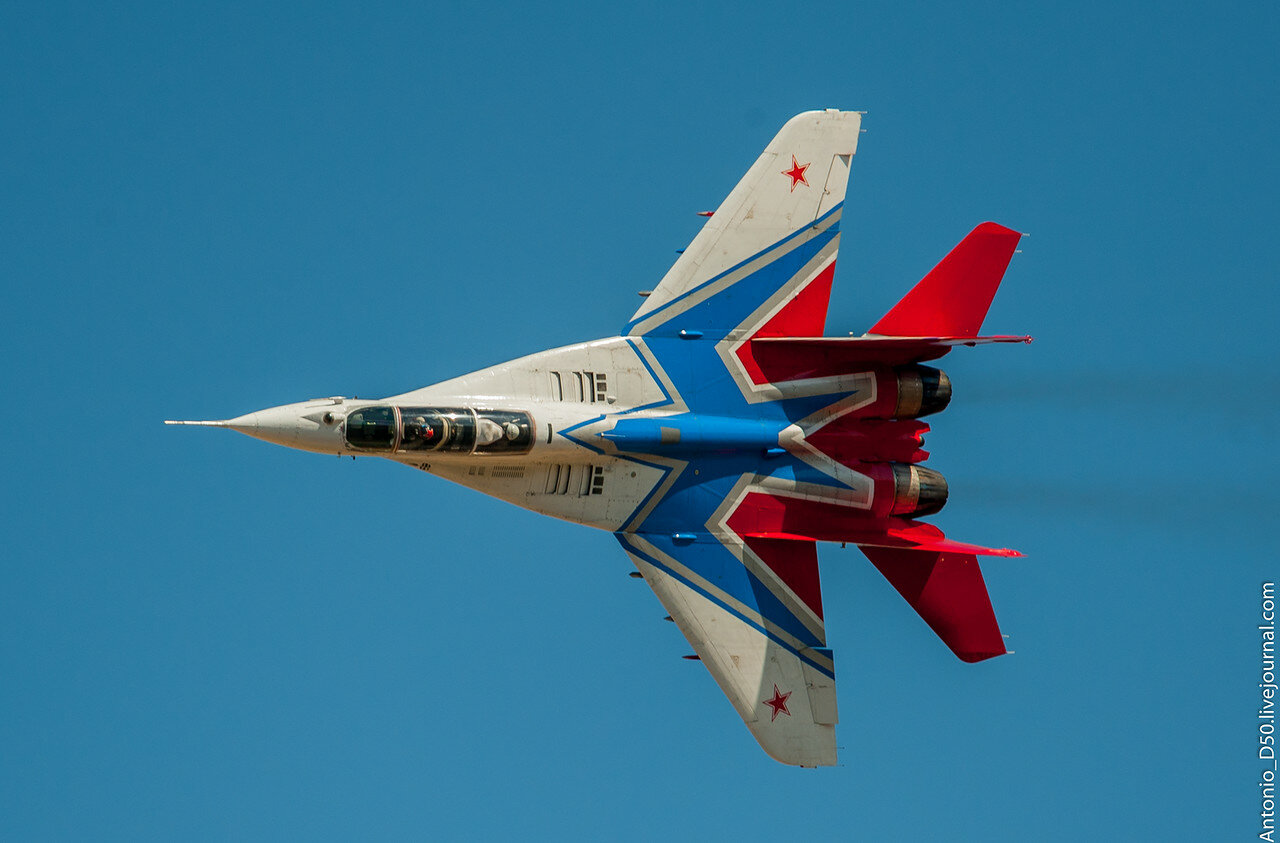
35.

36.
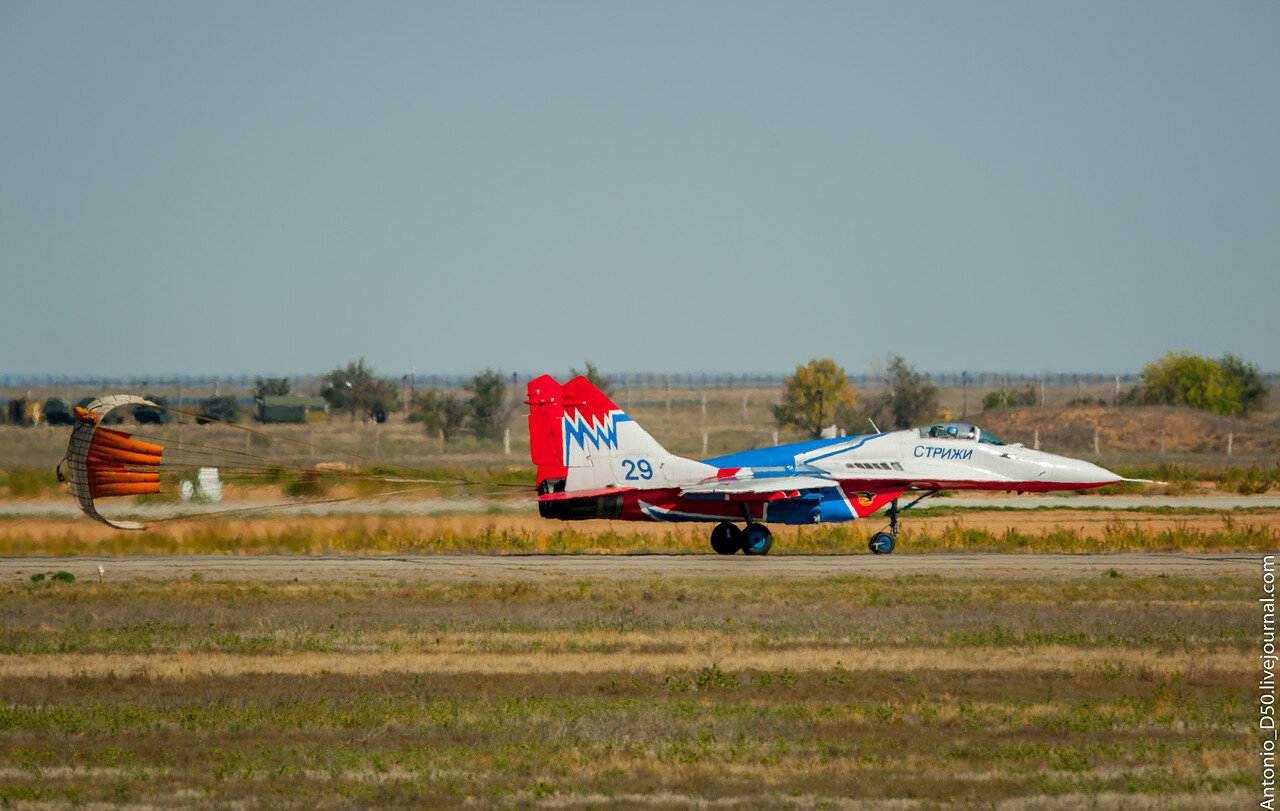
37.

26 сентября 2015.


19-го августа состоялось торжественное открытие Энгельсского локомотивного завода и вместе с открытием была представлена первая изготовленная на заводе секция нового двухсекционного электровоза 2ЭВ120 (2-секционный ЭлектроВоз, скорость 120 км/ч). Соответственно образец успели показать на Пятом Международном железнодорожном салоне «ЭКСПО 1520» ну и в общем до этого достаточно скудной информации о проекте стало побольше (первые фотографии, какая-то техническая информация и т.п.). Ну а на днях в составе блог-тура мне уже удалось побывать на самом заводе в Энгельсе и посмотреть на новый проект и этапы сборки своими глазами, о чём и спешу поделиться.
Но для начала всё-таки немного общей информации. Энгельсский локомотивный завод относится к Первой Локомотивной Компании - проект российских инвесторов и канадской компании Bombardier Inc. (один из крупнейших в мире машиностроительных компаний, специализирующихся в том числе и на производстве локомотивов).
В 2012-м году на окраине города Энгельс (Саратовская область), по сути дела на территории представляющую собой огромную несанкционированную свалку, на чали с нуля возвозить завод по по канадским технологиям. Назначение предприятия - выпуск магистральных грузовых электровозов нового поколения. Сейчас уже можно увидеть первые действующие образцы этого проекта - одна секция 2ЭВ120 уже готова, ещё три секции находятся в разной степени готовности, к концу года должны быть готова два двухсекционных локомтива, которые будут отправлены на сертификацию. По завершении всех сертификаций, к концу 2016-го должен начаться уже серийный выпуск электровоз для России и стран СНГ (да и вообще везде, где есть колея 1520 мм). Мощности завода позволяют выпускать в год до 150 локомотивов (300 секций).
Особенности нового локомотива:
- электровоз двойного питания (работает как на сетях переменного тока, так и на сетях постоянного) - в данный момент большая часть действующих в России электровозов заточена только под один тип сетей, из-за чего в местах стыков требуется замена локомотивов (например при движении из Саратов в стороны Москвы или Питера перемена с переменного на постоянный происходит на станциях Узуново или Рязань-2 - стоянка в среднем 30 минут)
- конструкционная скорость - 120 км/ч; мощность каждой секции - 9600 кВт; двухсекционный локомотив может тащить до 7200 тонн (стандартных 120 вагонов по 60 тонн)
- наличие вспомогательного дизель-генератора, т.н. «Дизель последней мили» - для маневровых работ. Как полноценный дизель-локомотив использовать не может, но порядка 3,7 км полный груженный состав может протащить в случае необходимости.
- экплуатационные температуры от -55 до +45.

Отправляемся на экскурсию по заводу. В данный момент он находится в состоянии пуско-наладки - в данный момент здесь работает инженерная фирма до окончания сертификации. Тем ни менее возведение всех корупсов уже завершилось, и хотя ещё не все станки до конца смонтированны (закупка и поставка уже полностью проведена, однако монтаж ещё не завершен), в данный момент на предприятии уже отсуществлен выпуск первых тестовых образцов.
На обширной территории завода очень чисто-аккуратно. Весь чернозём (вместе с обильно покрывающим его мусором, которые был до этого) был снят и уже на суглинке осуществлено строительство новых корпусов. Все коммуникации (электричество, вода, обогрев, кислород и углекислый газ для сварки) к ним идут преимущественно воздушным путём - проще эксплуатировать и обслуживать:



Начинаем осмотр с цеха изготовления рам тележек. Первые тележки изготоваливались на энгельскосском заводе ЗМК, однако в дальнейшем изготовление и комплекс 3D-измерений-тестирований будет производится здесь:

Специальное помещение для измерений с особым температурным контролем. Сверху сдвигается крыша и готовые изделия опускают туда краном:

В каждом цеху кстати достаточно много кранов. Интересно то, что управлять ими можно как из кабины сверху, так и снизу специальным пультом-джойстиком:

Инженер-крановщик демнстирует нам возможности именно второго типа управления, который имеет свои плюсы - можно точно позиционировать детали в станках-крепежах. Верхняя же кабина нужня для того, чтоб видеть весь зал целиком, так сказать "общую картину" - иногда полезно бывает управлять краном именно так:



Сборочно-сварочный цех, где готовятся рамы кузова:


Все заготовки отмечены и промаркированы:

Из таких вот небольших элементов свариваются элементы покрупнее, потом ещё больше и в итоге получаются огромные каркасы:



Нам демонстрируют один из станков для сборочно-сварочных работ: все детали сначала устанвливаются в специальные станки (которые для удобства работы ещё можно потом всяческие вращать), и только потом начинает осуществляться сварка:

А вот это уже готовая деталь:

Каждая сваренный элемент проверяется инженером Отдела Технического Контроля - у них там огромные журналы, где казалась бы простая боковина может проверяться по сотне разных параметров:

Везде различные схемы и чертежы. Какие-то достаточно наглядные, какие-то менее понятные:


Чем мне нравятся все эти заводы западного образца (известные по многичесленным программам на ТВ) - это т.н. "культурой производства". Везде чистота и порядок (хотя казалось бы производство не сказать, что стерильное - режут, шлифуют, варят. Тем ни менее везде инструменты на специальных стендах - сварочные аппараты и пылесосы если не используются - аккуратно стоят в сторонке:


Различные информационные стенды:

Пример работы со станком: деталь варится в одном положении, потом для удоства - чтоб не тянутся или не нагибаться - переворачивается в другое положение и продолжается работа:


Для удобства передвижения по территория (всё-таки огромные и ходить там от одного цеха до другого может быть достаточно долго) инженерами используются велосипеды. Такое уже приходилось видеть например на Саратовской ГЭС (где цех тоже имеет протяженность больше километра):



После окончания сборки рамы кузова и каркаса кузова локомотива - можно в случае возникновения каких-то небольших деформаций-вмятин использовать специальную электромагнитную листоправильную машину (правят погнутые листы):

Хотя большая часть кузова собирается здесь, крыша изготовливается отдельно (в данном проекте - из алюминия) и монтируется уже в самом конце, то же касается тележек:

Перемещение же по цехам корпуса происходит вот на такой технологической тележке, на которую корпус грузят после окончания сборки-проверки:

На этой тележке корпус попадает в трансбордерный цех.
Специальная машина трансбордер перемещает корпус по цеху, откуда он попадает в те или иные отсеки для проведения тех или иных работ. При перемещении по цеху, корпус вместе с тележкой находится внутри этой машины:




Цех дробеструйной обработки корпуса:

Цеха для грунтовочных и окрасочных работ:


В данный момент корпус одной из секций локомотива как раз находится в покраске:

Следующий этап - перемещение уже готового корпуса в цех конечно сборки, где в него производится установка уже всех агрегатов: пультов управления, силовых установок, компрессоров, трансформаторов и т.п.:
Здесь такое чувство, что не просто чисто - а вообще стерильно (попасть в цех можно либо в специальной обуви, либо в бахилах):

В этом цеху может осуществляться одновременная сборка 8 секций локомотивов:

В данный момент проект является поистине интернациональным - различные элементы закупаются не только в России, но и в Германии, Франции, Италии, Швейцарии и Польше.
Однако в данный момент активно планируется локализация - где-то 80-85% элементов будут производится-заказываться в России:


Интересный и крайне необходимый элемент - в каждой секции будет распологаться туалет, на месте осуществляющий температурную обработку отходов (ни запаха, ни каких-то выборосов - всё в пыль):


Элементы управления монтируются здесь же:


Монтаж токоприемников на крыше:


Комплектация одной из секций локомотива:










Пульт управления локомотива:


Установка на тележки производится уже в самом конце, после окончания монтажа:



Сразу же здесь проводится первый тест - локомотив должен пройти через эту габаритную рамку, дабы удовлетворять стандартам "РЖД":

А здесь, уже в тестовых цехах стоит секция локомотива за номером 001, которая демонстрировалась на выставке в Москве:



Внутри немного тесно (оно и понятно - не пассажирский вагон), однако передвигаться можно вполне неплохо, я по крайней мере прохожу нормально:

А вот кабина очень просторная и удобная:




Даже микроволновка и холодильник уже сразу предусмотрены. Одним словом мне прям очень нравится:

Проходим через склад - ещё один пример культуры производства - образцовые порядок и всё везде подписано:

Специальное лифтовое хранилище для мелких деталей. В зависимости от необходимости вызывается те или иные секции:



Ну а на другой стороне за цехами располагается испытательный полигон (виднеется ветка с контактной сетью - которая поначалу вызвала у меня большое удивление - всё-таки здесь железная дорога неэлектрифицирована - а оказывается это не РЖД):

Вот такой завод - пока можно сказать, что работает в тестовом режиме (в ожидании сертификации), однако сейчас уже способен выдавать полный производственный цикл. К концу же 2016-го должен заработать на полную мощность и обеспечить работой около 1700 специалистов. Кстати специально для одного из стимулов привлечения специалистов позади подстанции (которая кстати запитана от БАЭС и способна обеспечивать не только потребности завода, но и питать близлежащие посёлки) строятся 3 50 квартирных дома-малосемейки для работников завода:



Одним словом - восторг. Даже при том, что пока нет возможности наблюдать полную загруженность завода. И даже при том, что я очень люблю поезда (и кажется был бы рад при любом раскладе). Это действительно - очень такой современный завод того вида, что больше привыкаешь видеть в каких-то зарубежных рекламных проспектах, но никак не надеешься увидеть в окрестностях родного города. Очень важный проект для области и надеюсь для развития железнодорожной системы страны, да.
И да, огромное спасибо заместителю главного конструктора Гаркавенко Андрею Евгеньевичу за подробную экскурсию, руководству завода за согласование этой экскурсии и



В рамках блог-туров, посетили один из старейших действующих энергетических объектов не только Саратова, но и России в целом - Саратовскую ГРЭС. Хотя не все догадываются о немаленьком возрасте станции (и уж тем более значимости этого объекта в истории энергетики), видеть хотя бы со стороны её доводилось многим - все знают эти дымящие трубы в центре...
СарГРЭС расположена на улице Чернышевской (практически на пересечении с Радищева), рядом с Волгой. Собственно раньше весь объект назывался СаратовЭнерго, но после реформирования РАО ЕЭС - там всё разделилось на несколько организаций и теперь собственно сама станция - лишь часть комплекса.
Вот так например вид на станцию (со стороны высотки на Горького/Бахметьевской):

А так ГРЭС выглядит со стороны Волги:


Строительство станции началось в 1926 в рамках проекта ГОЭЛРО и уже в 1930-м году в эксплуатацию была введена первая очередь станции (на тот момент 3 котла и 2 турбогенератора). Последующие очереди вводились в 1932, 1941 и 1951 соответственно (по 2 котла и по одному турбогенератору). Таким образом СарГРЭС старше саратовской же ТЭЦ-1 на 4 году (1-я очередь ТЭЦ-1 была введена только в 1934):

Ленин перед главным зданием - неизменная дань тому времени - всё-таки План ГОЭЛРО возник ещё в начале 20-х годов при непосредственном участии (собственно фраза "Лампочка Ильича" имеет отношение именно к этом - электрификации всей страны):


Лично меня всегда занимал вопрос: в чем отличие ТЭЦ от ГРЭС (хотя бы и на примере Саратова - хотя я думаю в других городах ситуация будет такой же). И та и другая станция вырабатывает не только элетроэнергию и тепло для нужд населения, и та и другая работали изначально на угле, а потом перешли на газ (или вспомогательно мазут в случае крайней необходимости). Даже оборудование и компоновка котёл-турбина используется одинаковая (поперечная связь котлов).
Ответ прост: никакой разницы по сути нет! Просто ГРЭС (расшифровывается как государственная районная электрическая станция) в советские времена имели более высокий статус (государственная же) и более высокое подчинение. То есть при прочих равных данных ГРЭС (государственная) более статусная была чем ТЭС (городского подчинения).

Кстати выработка тепловой энергии (обогрев и горячая вода) для нужд горожан началась только в 1958 году. Изначально это была чисто электростанцией. Кстати есть ошибочное мнение, что выработка тепла на всех таких станциях - это такой побочный продукт, мол "некуда девать тепло - давайте будем дома отапливать". Выработка тепла и электроэнергии являются равноценными процессами (тем самым обеспечивают большее КПД всей станции).

Первым делом на станции проходит инструктаж по технике безопасности и узнаем какие-то общие сведения о самой станции:

Отправляемся на центральный щит управления, откуда осуществляется контроль за станцией.


Оборудование по большей части современное, помимо плановых и капитальных ремонтов, также происходит постепенно обновления всего оборудования. Наивно было бы думать, что всё тут осталось в нетронутом состоянии с 1930-го года - станция как живой организм постоянно обновлялась и менялась:


Хотя какие-то элементы с тех самых пор остались и хранятся, как например вот эти датчики и лампочка на них (хотя это не сколько рабочие элементы - сколько символ эпохи ГОЭЛРО, своего рода памятник - там самая Лампоча Ильича):


С центрального щита хорошо просматривается весь машинный зал. Всего здесь работает 5 парогенераторов суммарной мощностью в 54 МВт. Для сравнения например Балаковская АЭС вырабатывает 4000 МВт, Саратовская ТЭЦ-5 - 440 МВт. Не так много одним словом, однако для питания центральных районов (где практически не осталось промышленных объектов) этого вкупе с вырабатываем теплом вполне хватает:




Машинный зал встречает нас фреской с Лениным во всю стену (ох уж этот Ленин - неотступно следит за всей Советской энергетикой):


В целом - машинный зал выглядит достаточно обычно - какие-то элементы чуть более старые, какие-то чуть менее:

Вполне обычные элементы управления (если можно вообще назвать такие пульты обычными - поди разберись какие кнопки и датчики за что отвечают):


Много-много непонятных труб-механизмов, впрочем после БЭАС с их трубами-датчиками (заполняющими всю стену) меня уже сложно чем-либо удивить:


Кстати несмотря на более чем просторный зал, здесь мало того что очень шумно (ну это понятно - работающие турбины), так ещё и достаточно жарко. Пар, раскручивающий генераторы, разогревается более чем до 400 градусов:

"Электросила" (ныне "Силовые машины"



Ещё один символ времени - 39-й год выпуска:

Покинув машинный зал отправляемся в соседнее помещение - котельную:

Котельная - здесь расположены газовые котлы. Газ сжигается и разогревает воду до высокотемпературного пара, здесь же техническая вода подогревается, чтоб поступать в тепловые сети.
Ещё один интересный факт - СарГРЭС была первой в СССР станцией, перешедшей с угля на газ. Во время войны ДонБасс был потерян и начали возникать перебои с поставкой угля, а саратовским предприятиям требовалась бесперебойная работа (здесь располагались многие оборонные предприятия). Сначала попробовали нефть - но она оказалась не так удобно (очень много отходов), да и поставки каспийской нефти по Волге были не так уж безопасны (в 42-м году немцы вышли к Волге). Поэтому было принято решение переходить на газ - в кратчайшие сроки (два месяца) от Елшанского месторождение был построен газопровод, который обеспечил бесперебойными поставками топлива предприятие.
Собственно помимо газификации это ещё в дальнейшем стало толчком для развития газопроводной системы - Газпром начал зарождаться тоже из Саратовской области:



В общей сложности в котельной 9 котлов (турбогенераторов всего 5). В отличие от той же ТЭЦ-5 с блочной системой (один котёл - один генератор), здесь станция с поперечной связью котлов. Это значит, что пар например от первого котла может пойти к 5-му генератору и наоборот пар от 9-го котла может попасть в первый генератор. Такая разветвленная система позволяет лучше балансировать с мощностями, гибче регулировать работу, но чревато энергетическими потерями и более запутанной системой паропроводов. Собственно изначально станции строились с поперечной связью, а более современные сейчас именно блочного типа - было признано, что это более эффективно:



За кирпичной кладкой - печь (ближе подойти как-то страшновато - да и жарко очень):

В плане старое-новое котельная часть выглядит ещё более эклектично:
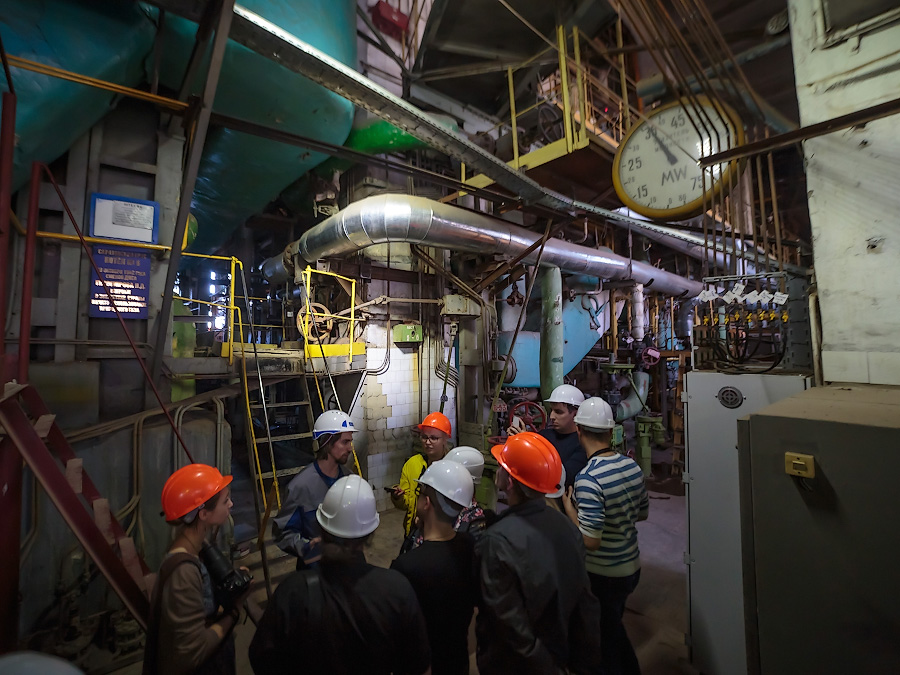

Вот например сохранившаяся угольная галерея - здесь сверху угольную пыль (измельченный уголь смешанный с воздухом) засыпали в печи - просто так поджечь уголь было достаточно проблематично - приходилось идти на такие технологические усложнения:


С переходом на газ необходимость в угле отпала - говорят одновременно было уволены почти 100 сотрудников - все люди занятые в техпроцессах подготавливающих уголь к сжиганию в печи (для примера общий персонал станции на данный момент около 200 человек):

Один из старейших котлов - той самой первой очереди, запущенной в 1930-м:

По соседству с ним котел №1 уже демонтировали и установили более современный аналог. Котел №2 следующий кандидат на замену:


На мой резонный вопрос: а является ли безопасным в плане эксплуатации столь старое оборудование, меня успокоили - каждый элемент регулярно подвергается проверке, и в случае необходимости ремонту или замене - соответственно всё сертифицированно и гарантийно работает. Какие-то элементы могут спокойно эксплуатироваться с 1930-го года, какие-то надо заменять раз в год - но в целом при правильной эксплуатации станция может прослужить ещё столько же.

То же самое про экологические нормы - на станции осуществляется жёсткий контроль всех выбросов, хотя газ сам по себе достаточно чистое топливо - по сравнению с тем же мазутом (который впрочем уже очень давно не использовали - хотя он подразумевается как резервно-аварийное топливо) и уже тем более углём.
Современное оборудование всё фиксирует:


В целом что хочется сказать.
Перед экскурсией у меня было глубокое убеждение, что СарГРЭС - это такой архаизм, отживающий своё и его надо плавно выводить из эксплуатации (как это сейчас постепенно происходит со станцией ТЭЦ-1). Но вот несмотря на весьма древний внешний вид, внутри станция вполне себе работоспособная и отвечающая всем современным нормам. Конечно можно возразить, что те же ТЭЦ-5 или ТЭЦ-2 (имеющие на порядок больше мощность) - могут легко закрыть все потребности, вызванные закрытием СарГРЭС - но пока что ни у кого нет ответа - что делать с инфраструктурой - электрическими и главное тепловыми сетями, ведь весь центр города завязан на СарГРЭС и только на неё, а в какой ад превратится город в случае перестройки тепловых сетей в центре даже представлять не хочется.
Одним словом - пока нет решения этого вопроса, СарГРЭС будет работать и работать вполне успешно!


Сегодня на летном поле и в заводских цехах стоит более 20 машин. Большинство из них были выпущены в 1985–1990 годах.
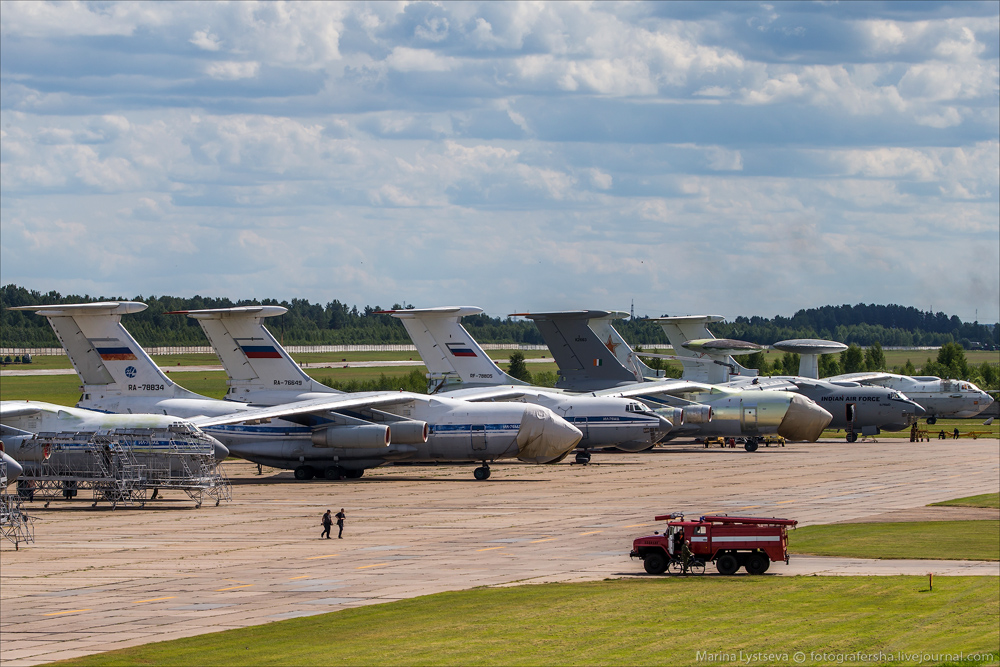
Срок службы Ил-76 на сегодняшний день – сорок лет. Перед специалистами завода стоит задача – разобрать воздушное судно, перебрать движки, выполнить необходимый ремонт, чтобы самолет мог надежно работать еще долгое время.

Только что прилетевшим на аэродром завода Илам предстоит провести здесь около пяти месяцев.

За это время с воздушного судна демонтируют агрегаты и двигатели, выполнят их ремонт, где потребуется, заменят начинку, заново покрасят, после чего будет установлен срок службы самолета до очередного ремонта, который составит 16 лет.


Большая часть машин предназначена для российских военно-воздушных сил (сегодня на вооружении ВВС состоит более 100 транспортных Ил-76).


Некоторые самолеты, специально доработанные под нужды иностранных заказчиков, улетят в Китай, Индию или Алжир.

Планируется, что выручка 123-АРЗ на 2015 год составит до 5 млрд рублей. По словам управляющего директора завода Андрея Сахарова, к августу текущего года завод выполнил до 80 % государственного заказа 2015 года.

Только за последние три года штат увеличился на 700 сотрудников – до 2 500 человек.
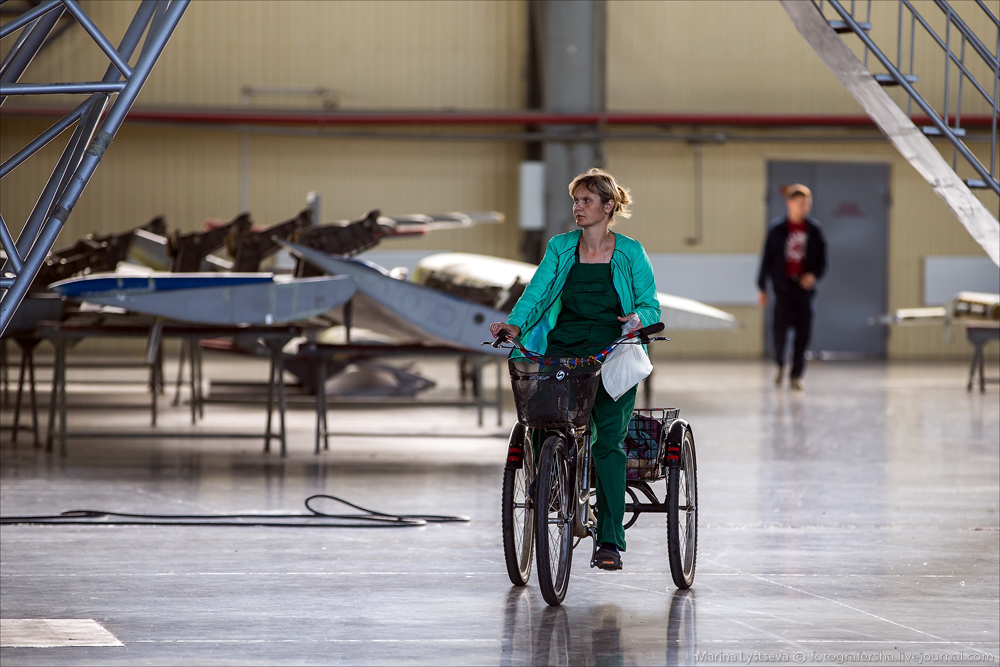
За несколько лет сотрудники предприятия смогли увеличить выручку в пять раз больше (по сравнению с 2000 годом) благодаря возрастающим объемам выпускаемой в рамках ГОЗ продукции и развитию экспортных программ.

В 1973 году Ташкентское авиационное производственное объединение им. В. П. Чкалова начало выпуск транспортно-десантных машин Ил-76.
Всего за годы работы выпустили около 950 самолетов. Более двух сотен из них до сих пор находится на службе российских вооруженных сил, часть числится во флоте частных авиакомпаний, остальные – у зарубежных заказчиков.
Производство Ил-76 в Ташкенте полностью прекращено в прошлом году, когда на доработку в Россию было отправлено два незавершенных борта. Зато у российских авиаремонтников фронт работ стал существенно расширяться.

Для того, чтобы избежать недоразумений с поставкой комплектующих – крепежей, кронштейнов, сот – в Старой Руссе постепенно разворачивается собственное производство отдельных деталей и агрегатов. Список наименований подобных деталей для самолетов уже занимает несколько десятков страниц.

Новое оборудование нужно и для других видов работ: ремонта двигателей, винтов и прочих изделий. Как показал опыт, собственное производство позволяет максимально удовлетворить потребности ремонта.

В этом году году на заводе завершили первую очередь модернизации: построили малярный корпус, на базе цеха механической обработки создали участок высокотехнологичного оборудования; также создали вертикальный обрабатывающий центр с уникальной возможностью обработки по 5 координатам для изготовления деталей сложной пространственной формы.
В большинстве цехов работы по реконструкции площадей либо еще идут, либо уже подходят к окончанию.
Перед покраской ненужные участки заклеивают бумагой.

Надписи внутри готовы к нанесению.

В малярном цеху начинается покраска деталей.

Завод постепенно внедряет программу импортозамещения. Около 60 % наиболее востребованных деталей уже изготавливаются собственными силами. Болты, гайки, прокладки – все раньше приходилось закупать у поставщиков. Теперь эта проблема решена. Например, более 4 тыс. наименований прокладок, которые используются для ремонта двигателей Д-30КП, в полном объеме производят на предприятии с помощью лазерных комплексов.
Имеющиеся резиновые детали во время капитального ремонта меняются полностью. Тем не менее, прежде чем пустить комплектующие в производство, необходимо пройти множество согласований с разработчиками и изготовителями – без письменного разрешения детали в серию не идут.
На заводе освоили и процесс изготовления стеклопакетов из ориентированного органического стекла, которые применяются на Ил-76. Ориентированное стекло – это разогретое при определенной температуре и растянутое по разным осям на заданную толщину особое стекло высокой прочности, и работа с ним требует профессиональных навыков.

На Ил-76 стоит порядка 88 стекол, и на каждое из них нужна своя пресс-форма. Для внутреннего и внешнего стекла они разные. Причем на предприятии собственными силами делают не только сами пресс-формы, но и стекла. Из 88 стекол на данный момент уже освоено 32.

К началу 2015 года на развитие производственно-технической базы и перевооружение производства было направлено более 2,1 млрд рублей. Эти средства пошли на строительство порядка 25 тыс. м2 новых производственных площадей, реконструкцию аэродрома, склада ГСМ, а также трех производственных корпусов цеха по ремонту самолетов Ил-76 и Л-410 с устройством в каждом корпусе наливных полов, модернизацией откатных ворот и инженерных коммуникаций.

В России сегодня летают десятки малых транспортных самолетов Л-410 чешского производства, которые, конечно, удобнее ремонтировать дома.

L410 в ангаре после испытательного полета.

Еще одним важным видом деятельности работы 123 АРЗ стал ремонт двигателей.
Несколько лет назад двигательное направление натолкнуло руководство на идею развить не совсем профильное для завода направление энергетики. Так, в Старой Руссе отслужившие свой срок двигатели АИ-20 переоборудовали для установок теплоэлектростанций. Вот уже несколько лет электричество и тепло предприятие не закупает на оптовом рынке энергетики, а производит самостоятельно, снабжая часть близлежащих кварталов.
На территории предприятия реализован ряд необычных идей в области промышленного дизайна, посмотреть на которые приезжают жители как родной Новгородской, так и соседних областей.
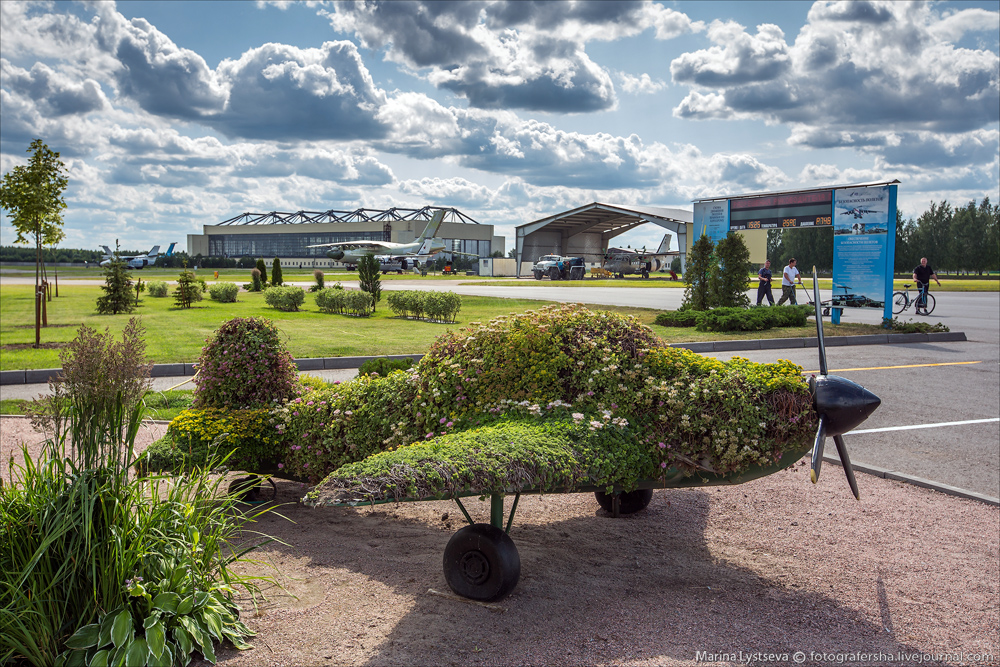
Также в последние время все больше туристов стараются совместить экскурсию по местам Достоевского, который работал в тарой Руссе над романами «Бесы», «Подросток» и «Братья Карамазовы» с посещением авиаремонтного завода.
Посмотреть на то, как осуществляется производство авиатехники, съезжаются не только представители различных промышленных предприятий, отдыхающие и школьники Новгородской области, но также жители Санкт-Петербурга, Москвы и других городов.
В течение года через музей завода проходит более тысячи экскурсантов.

За три прошедших года заводская территория преобразилась: появилась зеленая аллея, были установлены стальные макеты самолетов, выполнявших фигуры высшего пилотажа.
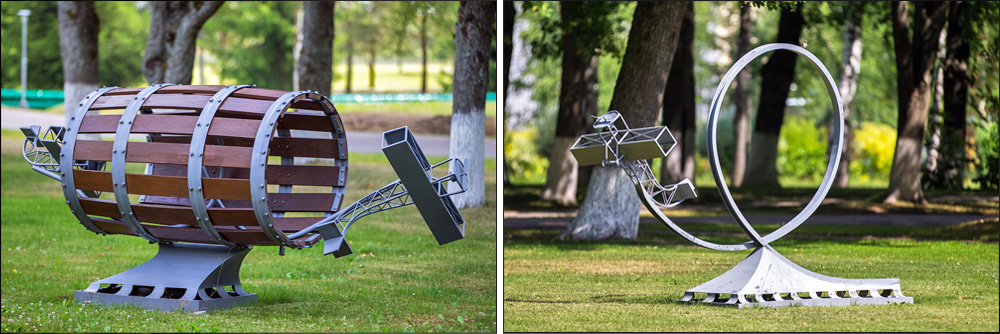

По правилам пожарной безопасности на территории предприятия находится много открытых водоемов. На самых больших рабочие установили фонтаны.

На сегодняшний день Россия и западные страны содержат сотни гражданских, военных и транспортных самолетов отечественного производства, срок эксплуатации которых составляет от двадцати до пятидесяти лет. Естественно, что каждое воздушное судно нуждается в периодическом ремонтном обслуживании.

Около года назад в состав ОАК вошло девять авиаремонтных предприятий, занимающихся ремонтом воздушных судов для министерства обороны и других ведомств.

Сегодня портфель заказов 123 АРЗ распланирован до 2025 года. Помимо транспортников Ил-76 здесь планируют обслуживать новые машины, например, модернизированные Ил-76-90-МДА, к выпуску которых ульяновский завод Авиастар-СП приступил в прошлом году.

Штурмовик Сухой Су-25БМ (Frogfoot) и его пилот с авиабазы Кант, Киргизия.
Штурмовик Су-25 выруливает на взлет.
На взлете штурмовик Сухой Су-25УБ.

Напомню, что в августе 2013 года, этот самолет временно экспонировался в музее, тогда УВАУ ГА отдало его музею лишь на несколько дней для проведения мероприятий посвященных дню Авиации.
(с) Юрий Дорошенко


Мне вновь удалось побывать на официальном споттинге (суть - наблюдение и съемка самолётов) в аэропорту Саратов Центральный, устроенным авиакомпанией "Саратовские Авиалинии". Траффик в Саратове не особо серьезный, но зато "Саратовские Авиалинии" к споттерам более чем лояльна: не только на споттинге покормили, но ещё возили-перемещали по полю в поисках наиболее интересных кадров взлёта-посадки самолётов. Одним словом споттинг получился достачно интенсивным и разнообразным.
Самым тяжким испытанием конечно стал подъем в 4 утра, дабы к 5 быть в аэпропорту - именно к этому времени был объявлен общий сбор: всего до съемок допустили около 25 человек (заявки на участие отправили больше сотни - всё-таки делалось всё официально - но вот всех желающих к сожалению пригласить не смогли). Причина такого раннего сбора - основные полёты происходят утром.
Embraer-195 Саратовских Авиалиний.
Провожаем Эмбраер в Москву:




Як-42Д Саратовских Авиалиний.
Быстренько перемещаемся к другому концу ВПП чтоб увидеть приземление Як-42, который прибыл из Екатеринбурга:


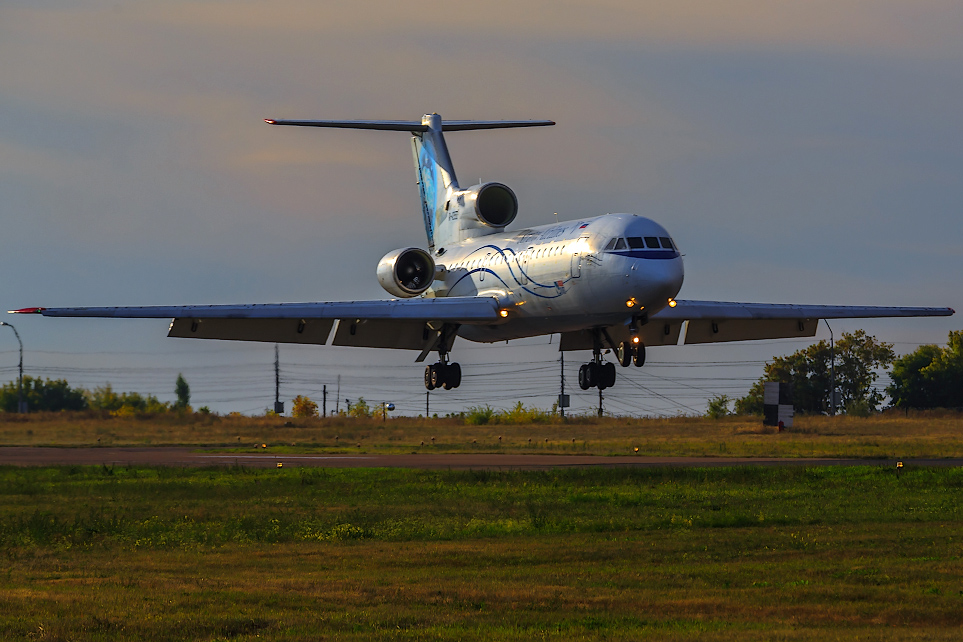


После небольшой стоянки/заправки Як-42 взлетает и отправляется уже в Москву:



Pilatus PC-12 Авиакомпании Декстер
Декстер по сути дела является таким аэротакси - используют небольшие одномоторные пилатусы вместительностью 2 человека экипажа и 8 пассажиров. Достаточно регулярно у нас появляются (в основном рейсы из Казани и Нижнего Новогорода и обратно):


Ми-8 Авиакомпания Газпромавиа
Попутно наблюдаем взлёт вертолёта - Газпром активно использует вертолёты для каких-то внутренних перелётов (так например у них есть своя площадка под вертолёт в Сторожевке). По началу меня в списке полётов смутило направление "Саратов - Саратов", однако увидев вертолёт всё стало понятно:


Заправившись и забрав новых пассажиров, Pilatus отправляется назад:

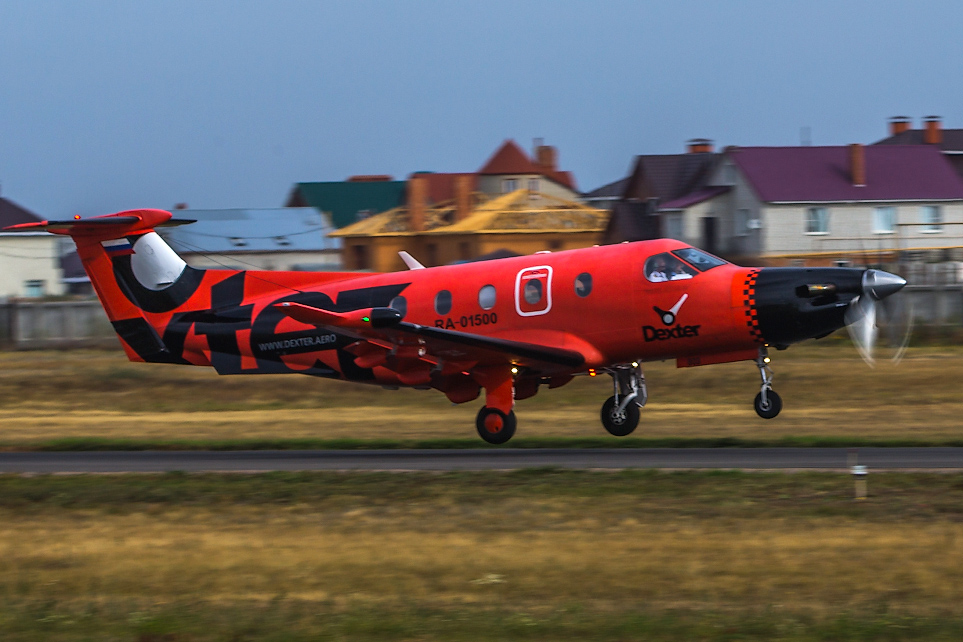

Тем временем Embraer-195 прибывает из Москвы.
Кстати взлетно-посадочная полоса аэропорта Саратов Центральный имеет небольшой уклон с востока на запад. С этой точки это особенно хорошо видно: момент касания ВПП самолётом не видно:



Л-410УВП-э авиакомпании Оренбуржье
Прибыл из Самары.


И опять-таки, сразу после небольшой стоянки-профилактики, забрав пассажиров - отправляется назад:


Embraer-195 вновь отправляется в путь, снова в Москву:




Embraer-145 компании Комиавиатранс
Сейчас появилась возможность летать из Саратова в Санкт-Петербург. Правда осуществляют перелёты не Саратовские Авиалинии, а компания Каомиавиатранс. Собственно данный рейс прибыл как раз из Санкт-Петербурга, но дальше из Саратова уже в Москву (после небольшой стоянки-профилактики):





Для людей, серьезно занимающихся споттингом (и снимающих скажем в московских аэропортах, или в тех же например Курумоче или Толмачево) - такой траффик может показаться весьма скудным. Однако для Саратова это очень даже крутой результат (пяток разных видов самолётов, десяток рейсов, разные ракурсы), короче я как начинающий споттер в восторге от этого.
Более того, надо ещё раз поблагодарить компанию Саратовские Авиалинии - они не только перемещали людей по полю в поисках интересных ракурсов (в течении утра, направление взлета-посадки менялось - поэтому удачное место съемки в одно время переставало быть таким спустя пару часов), но и в промежутках между рейсами устроили экскурсии в ангар и провели по салону одного из самолётов, и даже дали возможность поприсутствовать на учениях пожарных частей аэропорта - но об этом в следующий раз...



И ещё один объект, который удалось посетить в рамках нашего Хвалынского блог-тура - пожарная каланча. Здание постройки конца 19-го века до сих пор исполняет свои функции по назначению - здесь размещается пожарная часть (точнее говоря - службы МЧС). Сама башня само собой для пожарных нужд (вроде обзора окрестностей на предмет возгораний) не используется - зато может служить великолепной смотровой площадкой в центре города. Туда-то мы и направилсь.



Пройдя через дворик заходим внутрь здания и поднимаемся на второй этаж:



Дальше подъем на башню по винтовой лестницы. После пражских башенок и регулярного подъема на Исаакиевский собор - здесь очень светло, уютно и главное - невысоко:



Вот и обзорная площадка:


Ну и серия видов предрассветного Хвалынска:





















В моем блоге уже немало фоторассказов о самых разнообразных мельницах, но водяных среди них не так уж и много. Поэтому сегодняшний пост как раз о такой. Мельница находится на окраине села Красниково Курской области на речке Нагольненский Колодезь. Кстати, в сети эту речушку сплошь и рядом называют Крюком (реже - Ручей Широкий). Предположу, что это, скорее всего, устаревший местный гидроним, так как на всех картах река называется именно Нагольненский Колодезь либо Нагольненский Колодец. Кроме того, курские СМИ растиражировали версию о том, что это единственная сохранившаяся мельница подобного типа в Черноземье, но это тоже не верно. Но не суть. Побывал я в Красниково еще в мае, поэтому в преддверии золотой осени, решил сегодня порадовать читателей картинками свежей весенней зелени.
02. Всего несколько лет назад, не смотря на то, что в 2003 году по рекомендации Министерства культуры постановлением губернатора Курской области Красниковская мельница была включена в единый государственный реестр памятников истории и культуры народов РФ, находилась она в ужасном состоянии и попросту была опасна для посещения из-за крайней ветхости. В 2013 году мельница была отреставрирована (был перебран сруб мельницы и укреплен фундамент), расчищен пруд, поставлена беседка для отдыха и сделано плетеное ограждение. В 2014 году была проведена дополнительная работа по благоустройству окружающей территории, а так же проложена асфальтовая дорога с местом для парковки и туалетом. На эти цели было выделено 4,7 миллиона рублей.

03. Общий вид туристического комплекса (назовем его так) по состоянию на май 2015 года. Поясню по поводу некоторого хаоса на переднем плане. Это пни спиленных на этапе реконструкции деревьев. Не берусь судить, правильное ли это решение или поспешное, так как сам лично не видел мельницу в окружении старых вязов. В сети есть старые снимки места, вроде неплохо, но теперь уж как есть. Сейчас рядом с мельницей проходят встречи местных ветеранов, приходят встречать рассвет выпускники местной школы, приезжают туристы, да и вообще кипит жизнь.

04. Построена мельница в 1861 году местным помещиком Глазовым, о котором сведений практически не сохранилось. Но именно в "глазовские времена" была организована запруда на реке и забиты два десятка свай из мореного дуба, на которых мельница стоит до сих пор. А батраком у этого Глазова работал некто Фома Игнатьевич Тетянец, который в итоге стал новым хозяином глазовской мельницы. На этот счет в селе имеется две версии-легенды. По одной из них, помещик, почуяв в 1917 году грядущие перемены, просто распродал имущество и уехал заграницу, а по другой - досталась мельница Фоме в приданое, ибо имел тот наглость обрюхатить дочку помещика Софью прямо в ней.

05. Так или иначе, после революции мельница перешла во владение колхоза "40 лет Октября", а молодожены уехали к родственникам в Воронеж. Удивительное дело, но в начале двухтысячных в Красниково из под Самары приезжал на тот момент девяностолетний сын Фомы и Софьи - Степан Фомич Тетянец и рассказал, что и он и его родители всю жизнь с теплом вспоминали свою мельницу.

06. В 1960 году назначили мельником Красникова Егора Ивановича и под его началом мельница продолжала снабжать краснинцев мукой изумительного помола. До семидесятых годов прошлого века была на мельнице и крупорушка, но как перестал народ сеять на огородах просо и гречиху, а крупы стали покупать в сельпо, убрали за ненадобностью. А вот спрос на муку по-прежнему сохранялся. В девяностых колхоз приказал долго жить, но глава организованного СХП исправно выплачивал мельнику по 550 рублей зарплаты. А за помол одного мешка с мужиков брали по 7 рубликов.

07. При Красникове отжило своё старое старое мельничное колесо, но вскоре было заменено на металлическое и мельница заработала вновь (на этапе реконструкции оно было заменено снова на деревянное). Сруб здания тоже неоднократно обновлялся, а вот сам механизм, говорят, тот самый - глазовский. В день мельница производила до тонны муки.

08. Позже, когда поток помольщиков из близлежащих деревень и сёл иссяк, а самому мельнику стукнуло 77 лет, его назначили музейным работником, но сил присматривать за состоянием мельницы вскоре не осталось и она начала скоропостижно ветшать. Ну а дальше вы уже всё знаете. На фото обновленный т.н. погонный ларь.

09. В заключение немного собственных мыслей по поводу увиденного. Понимаю, что в наше время сумма в 5 миллионов - это сущий пустяк, особенно если учесть, что к мельнице подвели полкилометра асфальтовой дороги, но местами у меня сложилось впечатление некоей, так сказать, небрежности. Я видел реконструированные мельницы в Кенозерье и выглядят они совсем не так как на фото ниже (покажу в самое ближайшее время). Кроме того, здание мельницы огородили забором из сетки рабицы (виден на фото 04), что совершенно её не красит, но вынуждает туристов как-то его преодолеть.

Впрочем, зная ситуацию с мельницами родной Воронежской области, можно сказать, что Красниковской мельнице невероятно повезло. Наши ветряки не удосужились даже обвесить грозными табличками, не говоря уж о каких-то там реконструкциях или ремонтах. Как знать, переживут ли они эту зиму или нет, и поэтому поздравляю курян с тем, что у них в области сохранился такой замечательный исторический памятник!

Свою историю Лебединский ГОК ведёт с 20 июля 1967 года, именно в этот день было принято постановление Правительства СССР о строительстве в городе Губкин горно-обогатительного комбината на базе Лебединского месторождения железных руд Курской магнитной аномалии. В 1971 году был введен в эксплуатацию Лебединский кварцитный карьер, а уже в 1972 году ГОК дал стране свою первую продукцию - железорудный концентрат. В 1975 году была введена фабрика окомкования. В 1992 году комбинат прошел через приватизацию, а сейчас он работает в составе крупнейшего металлургического холдинга страны «МЕТАЛЛОИНВЕСТ». Знаменит он тем, что - это ведущий производитель и поставщик железорудной продукции и ГБЖ на глобальном рынке (мировой лидер в производстве товарного ГБЖ). Компания обладает вторыми по величине в мире разведанными запасами железной руды - около 14,6 млрд, 3-й в мире производитель окатышей и 5-й в мире производитель товарной железной руды.
2.

3. Ага, вот почему Лебединский! Классно они здесь припарковались.

4. Вот это и есть самый крупный в мире карьер по добыче железной руды, подтвержденные запасы составляют 3,9 млрд тонн. Что касается размеров, то его глубина где-то 450 м, а вот в диаметре он раскинулся на 4-5 км, и будет только увеличиваться. Разработка здесь ведётся открытым способом.
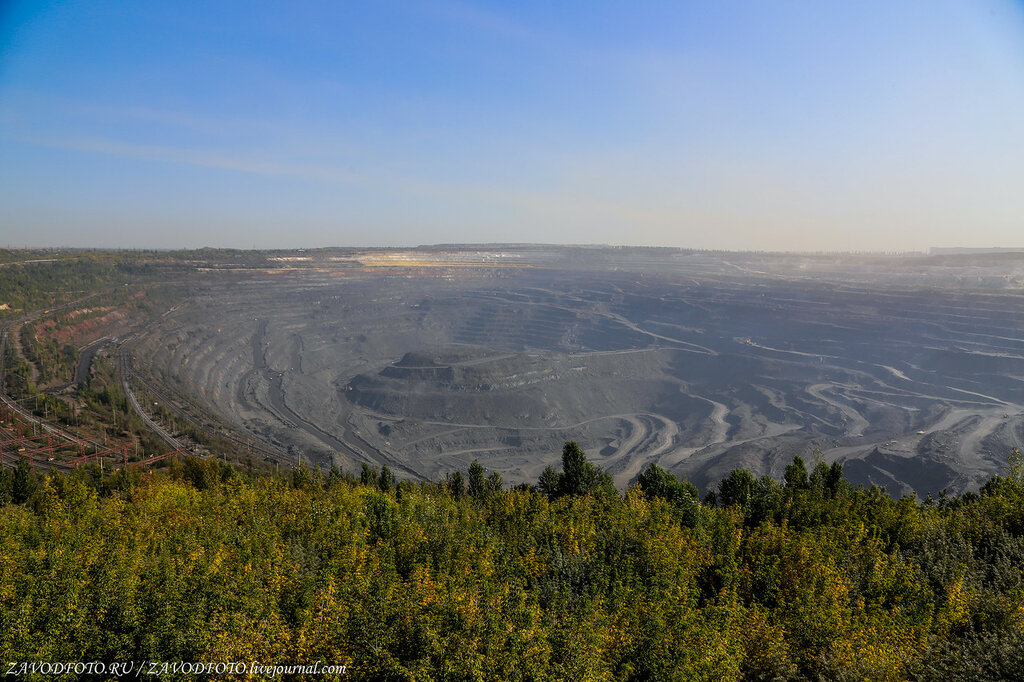
Очень жаль, что в этот день не проходили взрывные работы. Но ничего, переживем, вспомнить и без этого, конечно, есть что. Что касается всей технологической цепочки, то она начинается с бурения взрывных скважин. Ежедневно их объём здесь составляет 3,5 - 5 км взрывных скважин. Далее специальные машины заполняют эти скважины многокомпонентным взрывчатым веществом и Бах!!! После чего происходит экскавация взорванной горной массы из забоя на перегрузочный пункт, вначале автотранспортом, потом тут же на другом перегрузочном пункте его перегружают на локомотивосоставы. Далее она отправляется в корпус дробления, после чего уже на обогатительную фабрику.
5.

6.

7. В самом центре горка, это так называемый сланцевый язык, внутри пустая порода. В советское время, что было легко, доступно забрали вокруг, а это оставили на авось. Сейчас думают, как с этим справиться.

8. Гидравлический экскаватор HITACHI 5600, его ковшик (емкость ковша 23 куб.м.), как пол квартиры.

9.

10.

11.

12. А вот «думпкары», те самые ж/д вагоны, в которых возят руду с карьера. Грузоподъемность таких вагонов около 150 тонн, плюс они сами под 25 тонн весят. Около 350-ти км составляет длина железнодорожных путей на ГОКе.

13. На старой технике далеко не уедешь, поэтому в перманентом режиме её обновляют. Вот недавно закупились двумя такими красавцами-БелАЗами грузоподъёмностью по 220 тонн и 5 иностранцев купили из семейства Caterpillar грузоподъёмностью 180 тонн. Радует, что и отечественных производителей не забыли. Пять гусеничных бульдозеров тяжёлого класса Т-35 производства Чебоксарского завода «Четра» (помните, мы были у них в гостях: http://zavodfoto.livejournal.com/3528229.html ) тоже помогают стране добывать железо.

14. А ещё нам показали процесс, как с помощью водяной пушки происходит процесс разрушения стенок карьера.

Тоже самое только в движении.
15. Опять ЧЕТРА! Друзья должны пиарить друг друга


16. Люблю подмечать на заводах такие позитивные, солнечные истории и здесь их очень даже.

17. Такое большое производство - это целый город в городе, со своей инфраструктурой, тут даже своя церковь имеется.

18.

19. Постепенно мы добрались и до обогатительной фабрики. Это Цех №1 Лебединский ГОКа, где производится измельчение железной руды. Между прочим, самое длинное здание в этом царстве.

20. Привезённую сюда руду методом магнитной сепарации отделяют от пустой породы и измельчают до нужной крупности. После чего полученный железорудный концентрат отправляется на участок производства окатышей и ГБЖ. Железнорудный концентрат получается на выходе двух видов: с содержанием железа 66-68 % и с повышенным содержанием железа 69,5-70 %.

Так что же такое ГБЖ или Горячебрикетированное железо? А это высокачественное сырьё для производства стали, аналог лома, свободный от посторонних примесей. Между прочим, это самый чистый способ производства металлургического сырья. Массовая доля железа в нем составляет уже 90,2 - 90,7 %, степень металлизации - 93 %, и при этом в нём низкое содержание серы и фосфора.
21.

Более эффектно, как тут работают шаровые мельницы в нашем видео:
22. За всем этим добром следят на этом пульте управления, всё полностью автоматизировано.
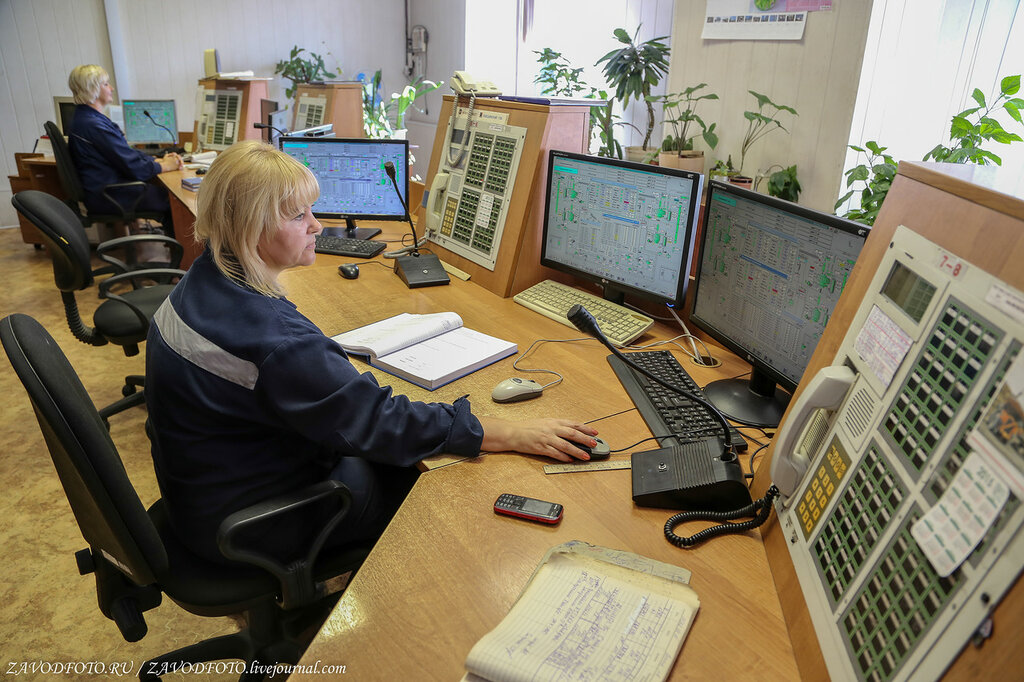
23. Следующий этап производственной цепочки проходит в корпусе Окомкования.

На этом участке наш концентрат проходит через обжиговую машину. Температура в зоне обжига достигает 1270 градусов С.

25.

26.

27.

28.

29.
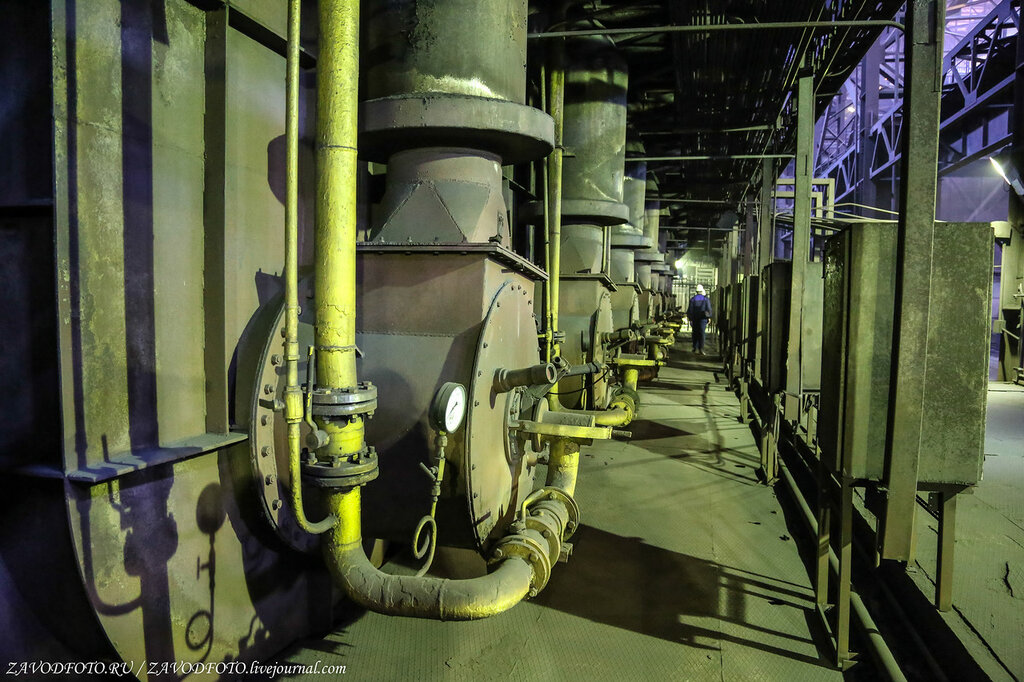
30. И далее на склад обожженных окатышей

31. Склад обожжённых окатышей

32.

33. Склад горячебрикетированного железа (ГБЖ)

34. Роторный заборщик в работе

35.

36. Вот это и есть конечный продукт Лебединского ГОКа, горячебрикетированное железо.

37.

38. Комплекс ЦГБЖ-2

Что больше всего радует глаз, что и здесь без стройки не обходится. Да ещё какой! Полным ходом идёт строительство третьего цеха горячебрикетированного железа, производственной мощностью 1,8 млн. тонн. Данный модуль по производству ГБЖ станет крупнейшим в мире. Ввод в эксплуатацию ЦГБЖ-3 намечен на декабрь 2016 года. Инвестиции в этот проект составят около 850 млн долл.
39.

40. Но главный инсайд нашего посещения, что основной бизнес это не металлургия, а то, что тут делают суперское мороженное! Так что будете в Губкине, воспользуйтесь возможностью насладиться этим вкусом.

Большое спасибо пресс-службе «МЕТАЛЛОИНВЕСТ» за возможность посетить такое уникальное предприятие!
Другие производственные подразделения холдинга «Металлоинвест», которые мы посетили:


P. S. Уважаемые собственники и акционеры, представители пресс-служб компаний, отделы маркетинга и другие заинтересованные лица, если на Вашем предприятие есть, что показать - "Как это делается и почему именно так!", мы всегда рады принять участие. Не стесняйтесь, пишите нам сами [email protected] и расскажите о себе, пригласив нас к ВАМ в гости. Берите пример с лидеров!
Уже около 150 промобъектов открыли перед нами свои двери, а вот и наши репортажи оттуда:
ПРОЕКТ: ZAVODFOTO - Шагает по стране! и ПРОЕКТ: «Пермский край - Нам есть чем гордиться!»

Относительно недавно в Липецкой области было 27 малых ГЭС суммарной мощностью 4000 кВт. Первую открыли еще в 1923 году у села Курапово, а после войны, когда как никогда была нужна электроэнергия, чтобы скорее восстановить народное хозяйство и вышло правительственное постановление «О развитии сельской электрификации», начали строить остальные. Эти электростанции строились на притоках и в верховьях Дона, а работа велась силами местных колхозов. Но уже в 70-х годах было принято решение подключить всю страну к высоковольтным магистральным линиям и малые ГЭС быстро остались не у дел. А потом развалились колхозы, на балансе которых они находились, и вот сегодня от большинства ГЭС не осталось и следа. Но кое-где живописные останки плотин и машинного зала можно наблюдать и поныне. Например, на реке Олым у села Борки.
02. Всё, что осталось от плотины.

03. Здание турбинного зала. Когда-то на этом месте стояла водяная мельница купца Новодережкина. Инициатором и руководителем строительства ГЭС был председатель Борковского сельсовета, бывший сотрудник охраны Сталина — Иван Ткаченко.
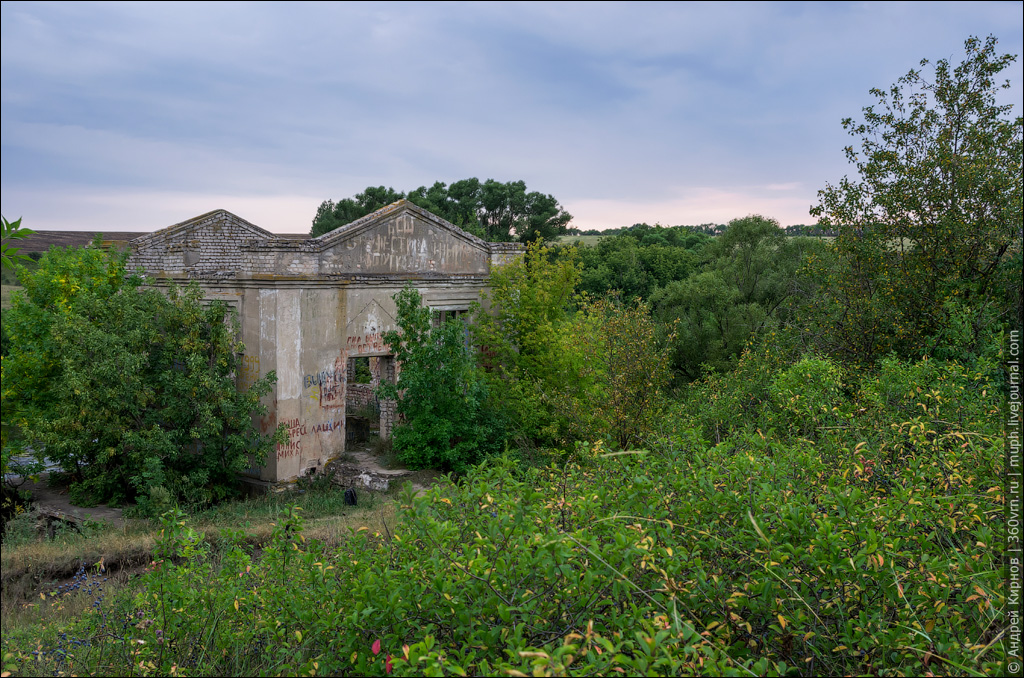
04. Вначале ГЭС выдавала электроэнергию для освещения ближайших жилых домов, производственных мастерских, новой мельницы и лесопилки. Чуть позже электричество пустили и в близлежащие к Боркам села.

05. На Борковской ГЭС было две турбины. Про мощность генераторов информации найти не удалось.

06. Кроме стен в здании ГЭС практически ничего не осталось. Интересно, что заставляет прямых потомков этих колхозников так усердно уничтожать построенное предками?

07. Олым почти на всем протяжении река очень мелкая и глядя сегодня на здание турбинного зала, стоящего на берегу и заросшего кустарником и деревьями, что когда-то глубина около плотины была такова, что с лодки тринадцатиметровым шестом не могли достать до дна.

08. Сейчас реку можно перейти пешком.

09. Да что там перейти! Переехать!

10. Даже на пузотерке. По крайней мере этим летом в августе это было под силу практически любому автомобилю. А главной сложностью была не сама река, а раздолбанный спуск к ней.

11. Вот так выглядит Борковская ГЭС сверху. За фото спасибо


12. Удивительно дело, когда коптеры были в тренде и стоили более или менее вменяемых денег, я совершенно не хотел себе такую игрушку. Ну вот не хотел и всё. А сейчас, когда их цена в рублях стала совсем уж неадекватной, я захотел такую приблуду и это желание нарастает всё сильнее с каждым днем. Максим любезно прислал мне rawки со своего фантома, я их покрутил и подумал, что, конечно, не айс, но жить можно. Ладно, внимание на фото. Вы не поверите, но вам крупно повезет, если на этом отрезке Олыма, вы найдете глубину хотя бы по пояс. А с виду ведь и не скажешь, правда? Переночевав вооон в той лесопосадке, на следующий день мы неоднократно переезжали Олым на машинах без каких либо проблем. И не только по плотине, но и просто так.

13. Вид на здание ГЭС с реки. Было бы здорово, если через несколько лет сюда пришли какие-нибудь молодые родители, и их ребенок, увидев эту красную надпись про выпуск 2008, сказал бы "Смотри, папа, какие-то нехорошие и глупые люди испортили стену краской", а папе вдруг станет стыдно, что это когда-то сделал он, хотя знал, что его дед и бабушка строили это здание и плотину, не жалея своих сил. Кстати, в сети полно статей со смелыми планами районной администрации о восстановлении Борковской ГЭС. Верится в это с трудом, но мало ли.

14. Просто артефакт времени в воде.

15. Какой-то странный круг под водой.

16. Поскольку у плотины было довольно людно, а вечер стремительно догорал, мы решили поехать поискать более уединенное местечко. И тут заметили вот такой знак и венок возле него.

17. А на другом берегу обнаружилась вот такая табличка. В 2011 году в районе ГЭС утонули два человека — девочка из лагеря «Спутник» и спасавшая ее вожатая. Студентка Елецкого педуниверситета Наталья Нечаева отправилась с детьми из тербунской коррекционной школы-интерната на прогулку. Ребята упросили вожатую дойти до гидроэлектростанции. Дети пошли по плотине и у 14-летней Нади Даниловой отстававшей в развитии слетел с ноги и уплыл сланец. Девочка прыгнула за ним в воду, а вожатая кинулась за ней. Дети рассказали, что Надя начала в воде паниковать, и Наталья не смогла с ней справиться. Взрослых поблизости не оказалось. Остальные дети помочь ничем не смогли. Узнав о случившемся, директор сам нырял за девочками, но вытащить их так и не смог. Нашли тела только водолазы.

18. Как я уже писал, Олым - река очень мелкая и в самом глубоком месте взрослому будет по грудь, но сильное течение у плотины вымыло яму. Это проклятое место, жертвами которого стали не только эти девочки. Поэтому, если поедете туда купаться как


19. Я же с утречка искупался чуть выше по течению Олыма. Без "джакузи", но тоже бодряще. А дальше мы поехали искать легендарный Конь-Камень. Но это уже совсем другая история.

Егоршинская ГРЭС. Почивший первенец плана ГОЭЛРО. Малоизвестный объект индустриального туризма
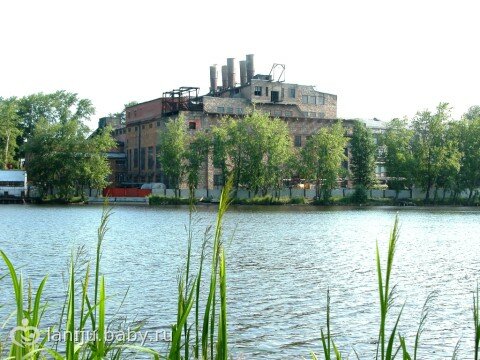
Строительство ее начал в 1913 году Е.П. Демидов вместе с угольной шахтой «София» на берегу реки Бобровка. Елим Павлович Демидов, сын Павла Павловича Демидова и княгини Марии Мещерской, унаследовавший от отца не только уральские заводы, но и титул князя Сан-Донато (Расцвет и упадок Сан-Донато. «Acta non verba» (Делами, а не словами)), служил по Министерству иностранных дел и вплоть до революции был посланником в Греции. В Россию после 1917 года не вернулся. Скончался в 1943 году в Афинах. И там же похоронен в приходе русской православной церкви.

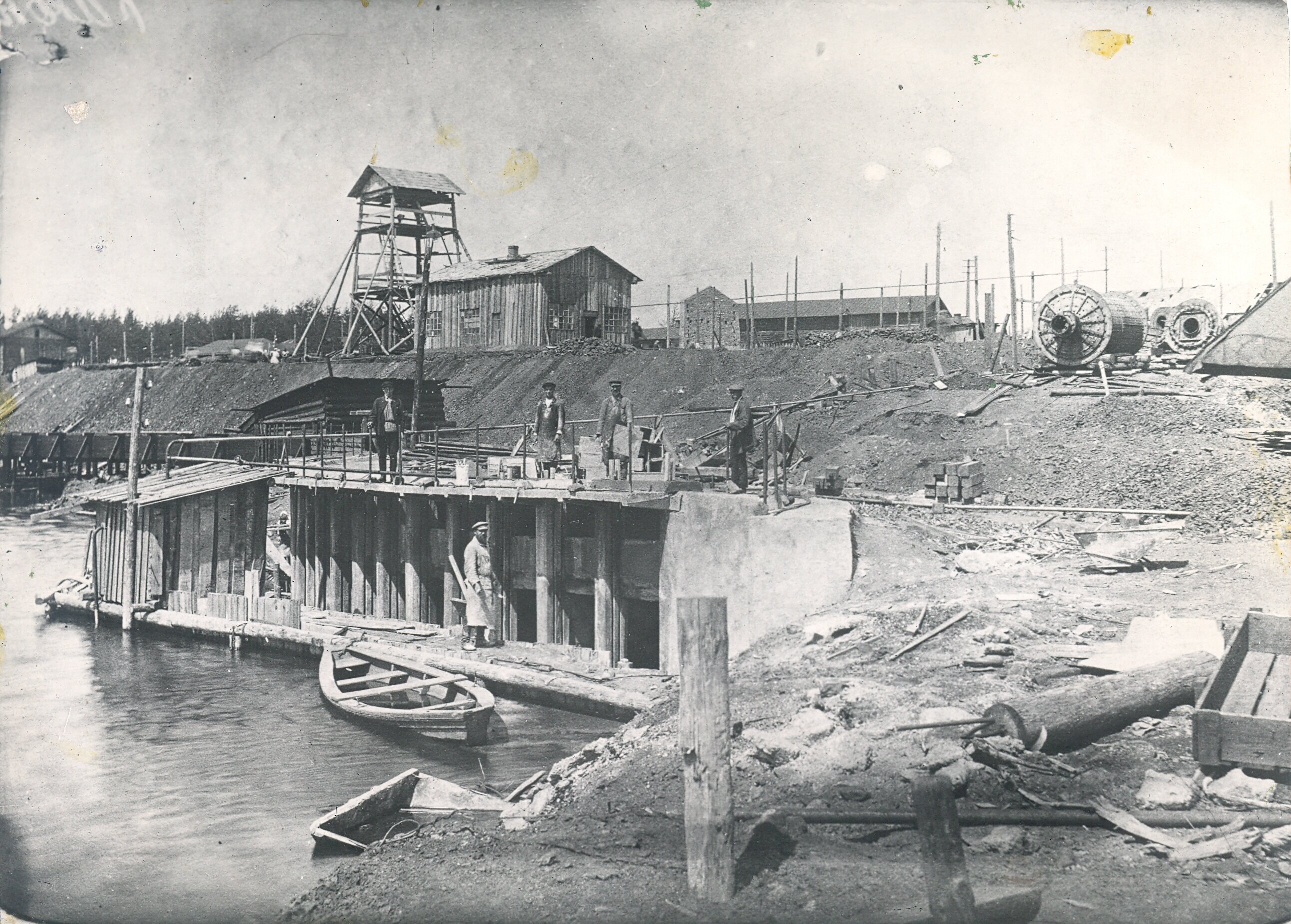
ЕГРЭС. Строительство.
Строительство электростанции было остановлено в связи с первой мировой войной и возобновлено только в 1920 году, когда объект включили в план ГОЭЛРО и признали ударным.
Уже в 1923 году электростанция дала первый электрический ток. Его вырабатывали два турбогенератора английского производства фирмы «Томсон-Хаустон» мощностью по 500 киловатт каждый. Позднее установили два более мощных турбоагрегата Ленинградского металлического завода и один шведской фирмы «Юнгстрем». А в 1931 году была завершена вторая очередь. Таким образом, к 1941 году станция имела установленную мощность 24 мегватта, а в годы Великой Отечественной войны ее мощность увеличили путем реконструкции на 20%.
Музей Егоршинской ГРЭС, любовно созданный и взлелеянный, хранит немало интереснейших экспонатов, в том числе подлинник справки об обследовании условий труда и жизни подростков, работавших во время войны. Перечислены 54 человека от 12 до 17 лет. Такая была рабочая сила.
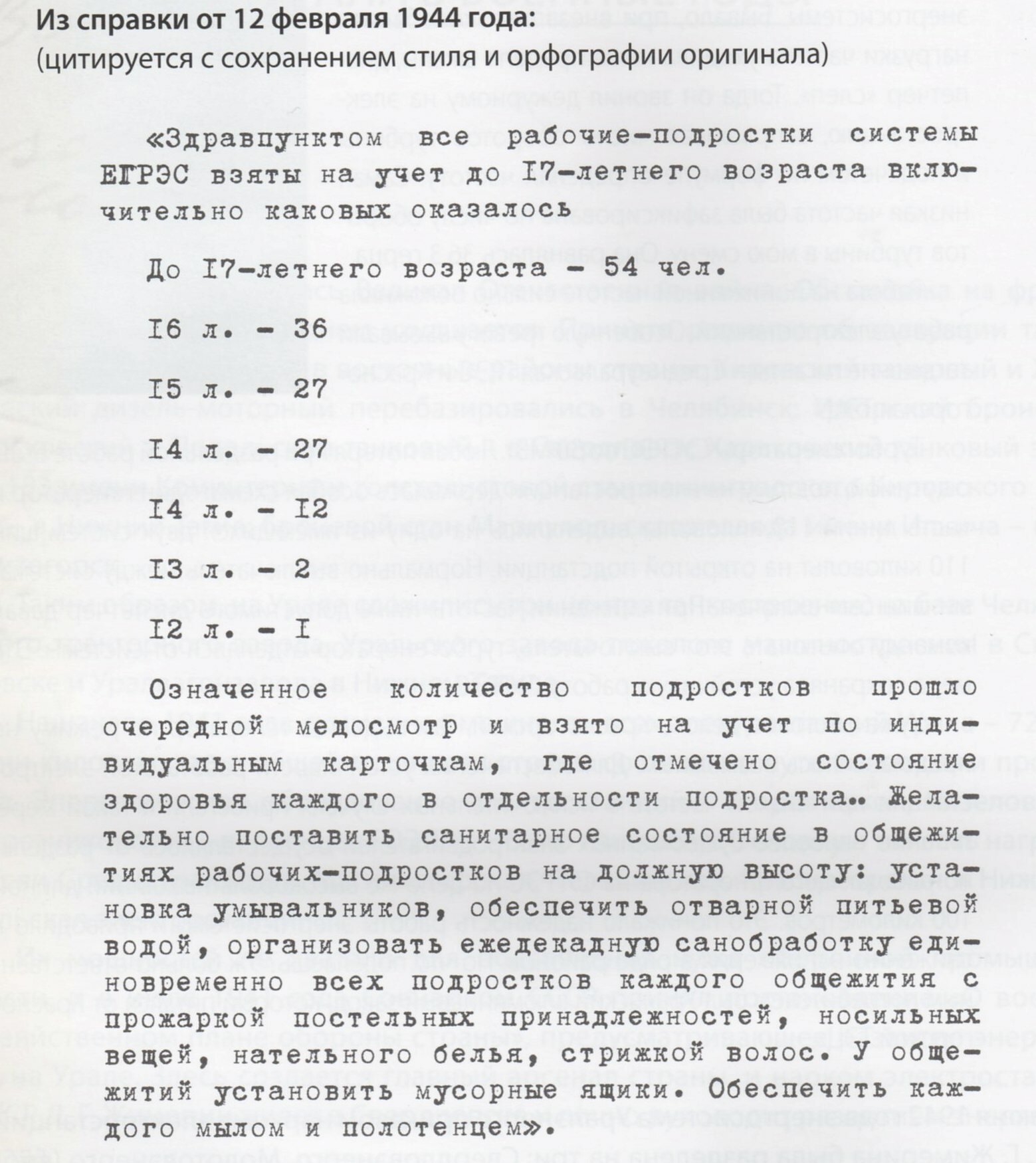
Из справки от 12 февраля 1944 года
В дальнейшем ЕГРЭС обеспечивала электроэнергией шахты в окрестностях Егоршино (Артемовского) и выдавала ток в Уральскую энергосистему.
Мощности ЕГРЭС начинают использоваться для теплофикации города. Первый шаг к этому был сделан в 1954 году, когда были проложены теплосети к части жилых домов работников станции.
Но в начале 1970-х гг. на Урале построены и введены в эксплуатацию новые энергетические мощности, в т.ч. Рефтинская ГРЭС. В этих условиях стремление к повышению выработки электрической энергии на ЕГРЭС потеряло смысл. Опыт теплофикации города послужил базой для использования станции как ТЭЦ. А с вводом в 1990 году современной Артемовской ТЭЦ неэкономичная, нетехнологичная ЕГРЭС не только утратила свое значение, но и стала для энергокомпании обузой.
28 октября 2003 года, в день своего 80-летия, электростанция в торжественной обстановке была остановлена.
Во многих источниках я читал, что ЕГРЭС причислена к историческим памятникам республиканского значения, однако, в опубликованном на сайте НПЦ по охране и использованию памятников истории и культуры Свердловской области списке Объектов культурного наследия, я его не нашел (http://www.patrimony.ru/page3/page14/).
В здании Егоршинской ГРЭС сохранилось не только остановленное промышленное оборудование, но организован музей.
Экспонатам, перевезенным сюда из Дворца культуры города, позавидовал бы любой краеведческий музей. Несколько лет музей держался на бескорыстном энтузиазме его заведующей Е.В. Корепановой. Но после реформирования энергетической отрасли Артемовская ТЭЦ не смогла содержать своего "старшего товарища". Музей поддерживается силами сотрудников МБУК Артемовского ГО "Артемовского исторического музея" (сайт музея - http://artmuzei.ru/, мои посты о нем - Артемовский. Место, где прошлое встречается с настоящим..., г.Артемовский. Музеицированный музей.), хоть и не является частопосещаемым. О нем в регионе, вообще, мало кто знает... Егоршинская ГРЭС не включена в туристические маршруты Среднего Урала.
Вот какими я увидел ГРЭС и музей энергетики:
Это не единственное в Свердловской области место, которое может стать привлекательным для индустриального туризма. О нижнетагильском Музее-заводе я рассказывал в посте О международном значении Нижнего Тагила! Такого больше нигде нет.... Самое интересное, что оба объекта являются первенцами, оба связаны с именем заводчиков Демидовых... Вот как неожиданно переплелись в нашем крае история людей и история промышленности...
В посте использованы материалы с сайта http://ejnews.ru

Недавно мне удалось попасть на экскурсию (спасибо

Мы посмотрели на то, как делают упаковку для молока и соков, а заодно нам рассказали про историю компании и про то, что еще она производит.
Делюсь впечатлениями
После войны в Европе остро встала проблема обеспечения населения долгохранящимися продуктами.
В 1951 году молодой инженер Рубен Раусинг основывает компанию AB Tetra Pak в г. Лунд, Швеция. В Лунде до сих пор находится штаб-квартира Tetra Pak.
А в сентябре 1952 первый упаковочный автомат Tetra Pak поставляется на молокозавод в Лунде.
Вот как это было (фото с сайта www.tetrapak.com)

Машина эта делала знаменитые «треугольники». Отсюда и название компании. А форма такая получилась, когда Рубен крутил в руках цилиндр из бумаги и смял его в форму тетраэдра.
У меня, кстати, тоже получилось

Первый раз в нашу страну Tetra Pak пришел ... угадаете? Мы не угадали. И даже с подсказкой про СССР не угадали.
А было это в 1959 году. Тогда был заключен первый контракт на поставку 8 упаковочных машин формата Tetra Classic, которые должны были паковать молоко в те самые, знакомые нам (тем кто родился в СССР) треугольнички. И сразу по залу шопот «Халтурщики! Кто не помнит, как они текли! Приходилось их перебирать, чтобы выбрать целый». Как оказалось, машины у нас быстренько скопировали, не заморачиваясь патентами и прочими авторскими правами, но скопировали некачественно. И вот продукция этих плохих копий - она то и текла по всем швам. На тот момент Tetra Pak пришлось уйти с рынка, контракт был расторгнут.
Второе пришествие - конец 80-х годов. В 1989 году в Москве появился офис Tetra Pak. Все начиналось с 3 человек, а сейчас административный аппарат насчитывает более 300 сотрудников. В 1991 году открылись офис и фабрика в Киеве.
В 2007 году была построена фабрика упаковки в Лобне, на которою мы и приехали в гости. Это крупнейшая фабрика компании в Восточной Европе.
Лозунг Tetra Pak «Сохраняем лучшее» относится не только к продуктам, но и к персоналу компании и к древесине из которой производится картон для упаковки.
Все сотрудники фабрики, а их около 300, питаются бесплатно в фабричной столовой (мы попробовали - очень достойно, намного лучше, чем в БЦ Нагатино, в котором я работаю, уж не говоря о том, что с меня за это безобразие еще и денег берут). На территории фабрики есть парковка и она также бесплатна (не в пример тому же БЦ). Я спросила большая ли очередь к ним на работу:
- Вы понимаете, у нас такая маленькая текучка, что как таковой очереди и нет. Но если место освобождается, да, желающих всегда много.
Из продуктов переработки упаковки Tetra Pak можно делать разные полезные вещи, например, покрытия для стадионов. Увы ,в нашей стране эта тема пока что крайне слабо развита.
А вот такая лавочка из переработанной упаковки стоит около главного входа
Фабрика участвует в программе воспроизводства древесины. Вся бумага, которая используется на фабрике, вырабатывается из сырья только тех лесных хозяйств, где нет сплошных вырубок, а взамен вырубленного высаживается такой же объем нового леса.
У фабрики более 220 партнеров по России. Это производители не только молока и соков, но и сыра, вина, мороженого, детского питания, кормов для животных и даже шоколада. Tetra Pak поставляет им не только саму упаковку, но и упаковочные линии, пастеризаторы и прочие комплексы для обработки продуктов питания. Компания может наладить полный цикл производства от сырья до упакованного продукта и осуществлять сервисное обслуживание оборудования.
Фабрика, на которую мы пришли в гости каждый день выпускает около 400 000 000 упаковок. Вернее заготовок под упаковки. Дальше они едут в цеха производителей продуктов и уже там превращаются в пакеты. И, хотя, вся упаковка дальше будет проходить обеззараживание, но и на самой фабрике Tetra Pak соблюдается довольно строгий режим. Для того, чтобы попасть внутрь, нас попросили оставить снаружи все сумки-рюкзаки и куртки. Одеть халаты и убрать волосы под шапочки. Снять часы и ювелирные украшения.
Заполнить анкеты про здоровье
И даже! Переобуться.
Я была приятно удивлена качеством предложенной обуви
Беглый взгляд на цех сверху
И мы идем в печатную мастерскую.
Тут готовят пленки для флексопечати
Каждая такая пленка - это один цвет
Принтеры, если эти огромные махины, что стоят в соседнем цеху можно так назвать, - рассчитаны на 6 основных и 1 пользовательский цвет.
Для справки: обычная печать, которой делают большую часть полиграфической продукции содержит 4 цвета.
Библиотека
Из печатного цеха мы идем в основное помещение. Оно довольно просторное, с широкими пустыми проходами между машинами - там работают автоматические погрузчики. Нас очень просили не попасть такому под колеса и гулять только
Рулоны бумаги ждут своей очереди в принтер. В таком рулоне 4,6 км бумаги.
Один литровый прямоугольный пакет - это 24,5 см.
Принтеров в цеху два. Длина каждого - 120 метров.
Максимальная скорость машины 600 м в минуту.
Вот эти «ворота» и есть принтер.
Обслуживают такую машину 4 оператора.
В рулоне бумаги потоньше 2 тонны веса и 13 км бумаги. Разумеется, она с разрывами, и поэтому каждая машина оборудована узлом склейки. В нем, с бешеной, скоростью (13 км за 20 минут) перематываются рулоны и склеиваются стыки
Отвлекаюсь на разноцветные лампочки
И приходится бежать 100-метровку, догоняя группу. Бежала вдоль принтера - это звучит красиво

Каждая секция печатает с одной пленки и один цвет.
Вот тут, очевидно, красный
Проверка печати
Опять отвлекаюсь
И снова перемотка в бобины
Теперь, когда картинка готова
Пора вспомнить из чего состоит наш пакет. Кроме картона (российского производства) и краски (на водной основе) нам еще понадобится алюминиевая фольга и полиэтиленовые гранулы (импортные). Каждый пакет будет состоять из 6 слоев
1. внешний слой - полиэтилен - защищает от влаги
2. картонный корпус - придает жесткость и форму
3. полиэтилен сваривающий бумагу с алюминиевой фольгой
4. фольга - защищает продукт от попадания света и воздуха
5. еще один связующий слой полиэтилена
6. слой пищевого полиэтилена для герметизации упаковки
Следующий этап - ламинатор. Это машина в которую засыпают гранулы, они там плавятся и на огромной скорости плавленный полиэтилен растекается по упаковочной поверхности. Примерно тоже самое происходит и с остальными слоями полиэтилена, не только с поверхностным. Перед ламинатором бобины снова перематывают и проверяют.
Ламинатор самая сложная и секретная машина в цеху и ее попросили не очень пристально фотографировать. Надеюсь, мне удалось.
Рубка управления
Максимальная скорость ламинатора 650 м в минуту. Его обслуживает 5 человек. Так как ламинатор нельзя остановить без потерь (ведь из него придется слить весь расплавленный полиэтилен - а это несколько тонн), то вся фабрика работает 24 часа, 7 дней в неделю. Рабочая смена 8 часов.
После склейки всех слоев - кстати, где они прячут фольгу я так и не увидела, рулоны разрезают на «плюшечки» шириной в один пакет, пакуют в термопленку и отправляют эти заготовки на заводы, где в них пакуют конечный продукт
Все операции расписаны по шагам
И кое-где на полу указано, какие именно тут шаги производятся
Ну и для антуражу
Отбракованная печать
Отработанные ведерки с краской
В цехах чисто, светло. Довольно шумно - персонал ходит в наушниках или берушах. Беруши можно взять на входе в цех - их там всем раздают. Там же нужно помыть или протереть дезинфекцией руки или же надеть перчатки. В цехах поддерживается определенная температура и влажность. Слегка тянет знакомым знакомым запахом.
- а что тут за запах такой, наверное химия - спросила одна из участниц экскурсии
- так ведь плавленым пакетом пахнет - осенило меня. И правда чувствуется не сильный, но ближе к ламинатору отчетливый запах плавящегося полиэтилена (туристы и те, кто случайно пришкваривал пакеты утюгом, - знают этот запах).
А перед входом, помимо сине-зеленой лавочки из пакетов (видна на заднем плане) стоит закладной камень
Жаль, что не удалось посмотреть, как из заготовок получается собственно упаковка, но это уже другие предприятия, а мы посмотрели то, что развернуто в Лобне.


Во время предыдущего визита на Балаковскую Атомную Станцию (посмотреть отчёт можно здесь: часть 1, часть 2 и часть 3), посетили практически все основные узлы станции. Однако по вполне логичной причине не попали внутрь реактора и спецкорпуса - это так называемые зоны ограниченного доступа: попасть туда можно только по специальному разрешению, а время пребывания стараются свести к минимуму.Собственно в зоны ограниченного доступа пускают далеко не всех сотрудников, а уж таких мы "туристов" вообще не пускают никогда. Но вот в данном случае для нас было сделано большое исключение и оказана большая часть. Так что уже только за такую возможность от меня большие благодарности всему руководству БАЭС, отдельно большое спасибо начальнику ЦОИ Дмитрию Сергеевичу Шевченко, и Никите

Итак, первым делом направляемся в специальный корпус, где переодеваемся в спецодежду (про средства защиты и вообще радиационного контроля расскажу в следующем посте), после чего по надземному переходу отправляемся в первый реактор АЭС. Собственно здесь уже и начинается зона ограниченного доступа. И хотя реактор вплотную примыкает к турбинному залу (образуя единый энергоблок) - попасть к реактору можно только таким путём:

В данный момент реактор находится на плановом ремонте (который кроме всего прочего включает в себя перегрузку топлива). В данный момент топливный цикл повышается до полутора лет (вместо года ранее). Собственно по причине остановки работы реактора (которая продлится 75 суток - капитальный ремонт) и появилась возможность попасть туда сторонним наблюдателям - во время работы вход туда предельно ограничен:



Вместо этажей здесь - высоты-отметки (0 - уровень земли, 36,9 - высота 36,9 метров над уровнем земли). Кстати точно такая же система обозначений и в расположенном по соседству турбинном зале


Помещения, где размещается смены реакторного отделения. Обычная смена включает в себя 4 человека и длится 6 часов - стараются свести пребывание в реакторе и количество инженеров к минимуму: все основные задачи выполняет автоматика, а общий контроль осуществляется с пульта управления энергоблоком. Задача же инженеров располагающихся здесь - контроль работоспособности систем и обход узлов реактора:





Поднимаемся на отметку 36,9 и отправляемся в сторону реакторного зала. Труба идущая под потолком - система вентиляции помещений:


Итак, наконец попадаем за гермооболочку, можно сказать в сердце АЭС - реакторный зал. Попасть туда можно только во время ремонта, когда реактор оставлен.

Хотя в теории относительно конструкции реактора всё более-менее просто и понятно, на практике первая реакция - удивление: зачем же здесь столько всего, все эти устройства.

Внизу видна верхняя часть крышки реактора. Сам реактор находится ниже и увидеть его возможности нет - он замурован в бетон:

По стене развешаны датчики:


Купол реактора (тот самый - который способен выдержать колоссальные нагрузки вплоть до падения самолёта и землетрясения). Также под потолком т.н. полярный кран:



устройство для закручивания гаек крышки реактора (по сути - герметизации):
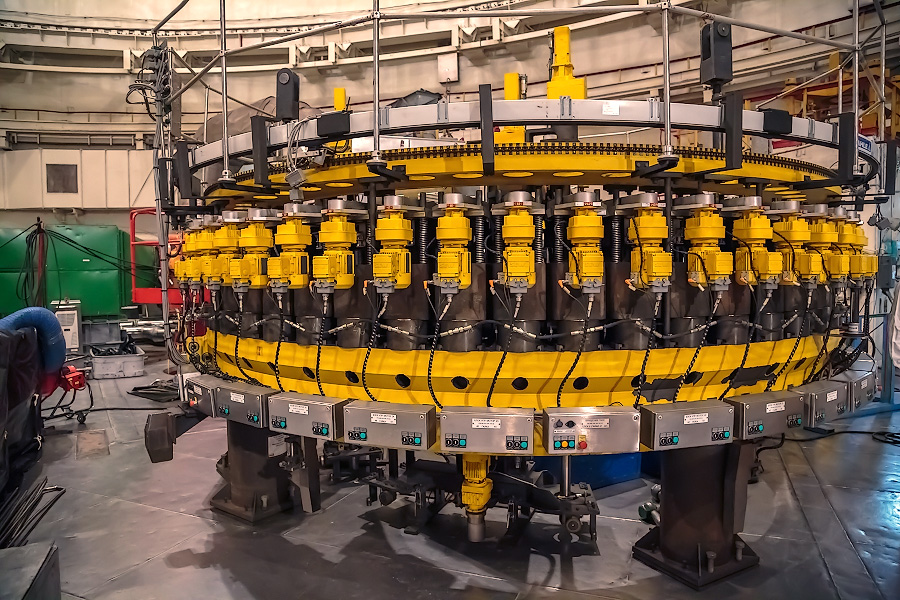
Перегрузочная машина - один из основных элементов использующихся для перегрузки топлива в реакторе:


Блок, размещающийся над реакторов - сюда помещаются датчики и системы управления и защитные элементы. Сейчас находится в полуразобранном состоянии:



Собственно многие элементы находятся в полуразобранном состоянии - ремонтные работы идут полным ходом:







Переодически глаз натыкается на опасные значки. Конечно использующиеся сейчас системы отчистки практически полностью исключают возможность случайного заражения, но лучше всё равно быть аккуратным - лишний раз не хвататься за поверхности, не заходить за ограждения и т.п.


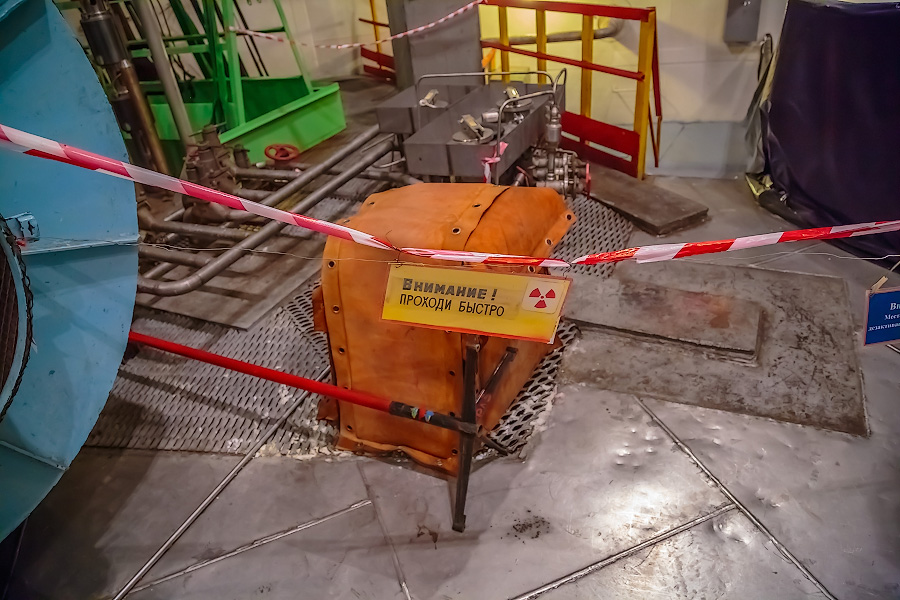
Старые, но всё ещё служащие приборы:


Покинув реакторный зал отправляемся на отметку -4.2
Здесь располагается различное вспомогательное и контрольное оборудование:


На первый взгляд это всё кажется каким-то хаотичным нагромождением слесарных деталей, просто так развешанных по стене:




Но всё это элементы контроля, обеспечивающие автоматическую работу всей системы в целом. Для контроля обычно хватает пары инженеров, которые полностью осуществляют обход за смену:




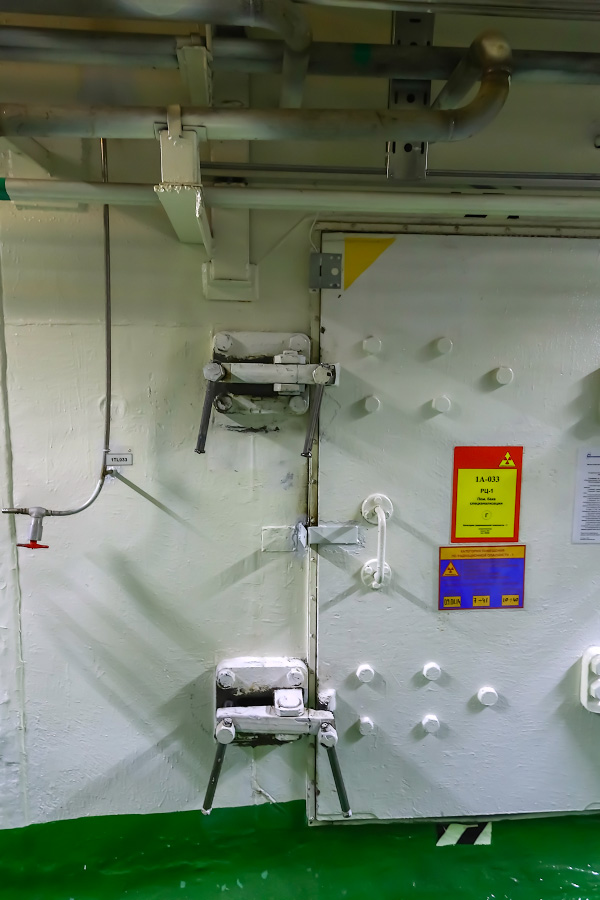
А вообще это в теории только всё просто "в реакторе разогревается вода первого контура..."
На практике это разумеется очень сложная многоступенчатая структура со всевозможными мыслимыми и немыслимыми система засчиты и резервирования:



Скажем вот например, система подачи воды для охлаждения. На каждом реакторе (как и большинство элементов) имеется в тройном экземпляре: один работает, один запасной и один если надо ремонтируется (или тоже как запасной ожидает своей очереди):



Во время посещения учебного центра АЭС уже успели ужаснуться количество знаний в виде томов, которым заставлены - необходимая информация, которой должно обладать оператор пульта управления энергоблока. Так вот судя по количество всевозможных элементов, у инженера смены работающей на реакторе знаний должно быть ничуть не меньше. Но и понятно, что вся это сложность в конечном итоге направленна на одну цель: обеспечить максимальную безопасность и бесперебойность работы станции...


1.Укороченный взлёт.

2.

3.

4.

5.Бочка на взлете.

6.

7.

8.

9.Видна работа ПГО и управляемых сопел двигателей.

10.

11.

12.

13.

14.

15.

26 сентября 2015


НКС СССР, или Народный комиссариат связи СССР, или Наркомсвязь СССР. Существовал Наркомат в 1932-1946 годах. Занимался вопросами связи, почты и телеграфа. 15 марта 1946 года Наркомат был преобразован в Министерство связи СССР.
Такой люк пока еще не попадал в объектив фотокамеры вообще. Среди многочисленных альбомов канализационных люков, я такого не встречал. Две штуки находятся буквально в 15 метрах друг от друга. Оба люка находятся на территории Тимрязевской академии.

Люк хорошо известного дизайна находится на Беговой улице.

А где этот не помню, но их в Москве много. Надпись Н.К.С. с точками. С какого времени перестали ставить точки в абревиатурах понять сложно. В начале 20-х годов абревиатуры С.С.С.Р. и Р.С.Ф.С.Р. писались с точками. Ближе к концу 20-х точки исчезли, написание стало привычным без точек СССР и РСФСР. Не знаю какими правилами русского языка регулировалось использование точек в абревиатурах.

А этот люк, сюдя по его дизайнерскому минимализму, наверняка выпущен в военные годы. Пока не найду аргументированную датировку, люк будет числится у меня как НКСовский. Обнаружен на Малой Ордынке.

Старая Басманная улица.

Новослободская улица.

Потаповский переулок.

Люк во дворе жилого дома на Дмитровском шоссе.

Напротив прокуратуры Московской области. Малый Кисельный переулок.

Люк такой же бочкообразной формы, но существенно отличается от предыдущего. Во первых, наличием надписи ТЕЛЕФОН НКС, а, во вторых, другой пространственной ориентацией «паучка». Люк обнаружен на углу Стромынки и Бабаевской улицы.

ВДНХ. А здесь «паучек» развернут на 180 градусов относительно надписи.
Господа! Иногда смотрите под ноги!


Канализационный люк торгового дома господ инженеров Паперно и Корецкого обнаружен на территории Покровской церкви на Нижней Красносельской улице. Там, во дворе, есть еще один точно такой же. А около входа, на улице, третий, но совершенно убитый, даже надпись «Паперно и Корецкий» практически не читается.